Cono de la máquina


Un cono de máquina es un sistema para asegurar herramientas de corte o portaherramientas en el husillo de una máquina herramienta o herramienta eléctrica. Un miembro macho de forma cónica (es decir, con un cono) encaja en el casquillo hembra, que tiene un cono correspondiente de igual ángulo.
Casi todos los husillos de máquinas herramienta, y muchos husillos de herramientas eléctricas, tienen un cono como método principal de fijación de herramientas. Incluso en muchos taladros de banco, taladros manuales y tornos que tienen portabrocas (como un portabrocas o un portabrocas), el portabrocas está sujeto mediante un cono. En taladros, taladradoras y fresadoras, el miembro macho es el vástago de la herramienta o el vástago del portaherramientas, y el casquillo hembra es integral con el husillo. En los tornos, el macho puede pertenecer a la herramienta o al husillo; las narices del huso pueden tener conos macho, conos hembra o ambos.
Explicación
Los operadores de máquinas herramienta deben poder instalar o quitar brocas de herramientas de forma rápida y sencilla. Un torno, por ejemplo, tiene un husillo giratorio en su cabezal, al que se le puede montar un accionamiento recto o trabajar con una pinza. Otro ejemplo es un taladro de columna, al que un operador puede querer montar una broca directamente o utilizando un portabrocas.
Prácticamente todas las fresadoras, desde las máquinas manuales más antiguas hasta las máquinas CNC más modernas, utilizan herramientas guiadas sobre una superficie cónica.
El cono de máquina es un sistema de montaje de herramientas simple, de bajo costo, altamente repetible y versátil. Proporciona indexabilidad, ya que las herramientas se pueden cambiar rápidamente pero están ubicadas con precisión tanto concéntrica como axialmente por el cono. También permite la transmisión de alta potencia a través de la interfaz, necesaria para el fresado.
Los conos de las máquinas se pueden agrupar en clases autosujetante y autoliberante. Con los conos autosujetantes, el macho y la hembra se calzan y se unen entre sí hasta el punto de que las fuerzas de perforación pueden resistirse sin una barra de tiro, y la herramienta permanecerá en el husillo cuando esté inactiva. Se extrae con una cuña cuando es necesario cambiar de herramienta. Los conos Morse y Jacobs son un ejemplo de la variedad autosuficiente. Con los conos de liberación automática, el macho no se clavará en la hembra sin una barra de tiro que lo sujete allí. Sin embargo, con una buena fuerza de tracción, queda muy sólidamente inmóvil. NMTB/CAT, BT y HSK son ejemplos de la variedad de liberación automática.
Para cargas ligeras (como encontradas por un torno de cola o una prensa de taladro), las herramientas con punteros de autocontención simplemente se deslizan hacia o hacia el husillo; la presión de la husillo contra la pieza conduce la manivela cónica firmemente en el agujero cónico. La fricción en toda la superficie de la interfaz proporciona una gran cantidad de transmisión de torque, de modo que no se requieran líneas o teclas.
Para uso con cargas pesadas (como las que encuentra el husillo de una fresadora), generalmente hay una llave para evitar la rotación y/o una sección roscada, que se acopla mediante una barra de tiro que se acopla a las roscas o a la cabeza de una tire del perno que está atornillado en ellos. Luego se aprieta la barra de tiro, introduciendo el vástago firmemente en el husillo. La barra de tracción es importante en las fresadoras, ya que, de lo contrario, la componente de fuerza transversal haría que la herramienta se saliera del cono.
Todos los conos de las máquinas son sensibles a astillas, mellas (abolladuras) y suciedad. No se ubicarán con precisión, y la variedad autosujetante no se sujetará de manera confiable, si tales problemas interfieren con el asiento del macho en la hembra con contacto firme sobre toda la superficie cónica. Los maquinistas están capacitados para mantener limpios los conos y manipularlos de manera que eviten que otras herramientas los corten. Los ciclos de cambio de herramientas CNC generalmente incluyen una ráfaga de aire comprimido mientras se cambia un portaherramientas por el siguiente. El chorro de aire tiende a eliminar las virutas que, de otro modo, podrían terminar interfiriendo entre el portaherramientas y el husillo.
Usar
Las herramientas con mango cónico se insertan en un casquillo cónico correspondiente y se empujan o giran en su lugar. Luego son retenidos por fricción. En algunos casos, es necesario fortalecer el ajuste por fricción, como ocurre con el uso de una barra de tiro, esencialmente un perno largo que sujeta la herramienta en el casquillo con más fuerza de la que es posible por otros medios.
La precaución debe ser ejercida en la máquina de perforación habitual o la situación de torno, lo que no proporciona barra de empuje para hacer que el cinturista entre en el compromiso, si una herramienta se utiliza requiriendo un par alto pero proporcionando poca resistencia axial. Un ejemplo sería el uso de un taladro de gran diámetro para agrandar ligeramente un agujero existente. En esta situación, puede haber una carga rotativa considerable. En cambio, la acción de corte requerirá muy poca fuerza de empuje o de alimentación. Thrust ayuda a mantener el tapiz sentado y proporciona un acoplamiento friccional esencial.
La espiga no está diseñada para soportar fuerzas de torsión que sean suficientes para provocar que el cono se deslice y, con frecuencia, se romperá en esta situación. Esto permitirá que la herramienta gire en el cono hembra, lo que probablemente la dañe. Hay escariadores de cono Morse disponibles para aliviar daños menores.
Vástagos cónicos "palo" Es mejor colocarlo en un encaje cuando tanto el vástago como el encaje estén limpios. Los vástagos se pueden limpiar con un paño, pero los encajes, al ser profundos e inaccesibles, se limpian mejor con una herramienta de limpieza cónica especializada que se inserta, se gira y se retira.
Las herramientas de mango cónico se retiran de un casquillo mediante diferentes métodos, según el diseño del casquillo. En taladradoras y herramientas similares, la herramienta se retira insertando un bloque de metal en forma de cuña llamado "deriva" en un orificio transversal de forma rectangular a través del casquillo y golpéelo. A medida que la sección transversal del punzón aumenta cuando el punzón se introduce más, el resultado es que el punzón, al apoyarse contra el borde más delantero de la espiga, empuja la herramienta hacia afuera. En muchos contrapuntos de torno, la herramienta se retira retirando completamente la caña dentro del contrapunto, lo que coloca la herramienta contra el extremo del tornillo de avance o un perno interno, separando el cono y liberando la herramienta. Cuando la herramienta está retenida por una barra de tiro, como en algunos husillos de molino, la barra de tiro se desenrosca parcialmente con una llave y luego se golpea con un martillo, lo que separa el cono, momento en el cual la herramienta se puede desenroscar y retirar aún más. Algunos husillos de fresado tienen una barra de tiro cautiva que expulsa la herramienta cuando se desenrosca activamente más allá de la etapa suelta; estos no requieren golpecitos. Para casquillos simples con acceso abierto al extremo posterior, se inserta un punzón axialmente desde atrás y se saca la herramienta.
Tipos
Existen muchos conos estándar, que se diferencian según lo siguiente:
- el diámetro en el pequeño extremo del cono truncado ("el diámetro menor")
- el diámetro en el extremo grande del cono truncado ("el diámetro mayor") y
- la distancia axial entre los dos extremos del cono truncado.
Los estándares se agrupan en familias que pueden incluir diferentes tamaños. La reducción gradual dentro de una familia puede ser consistente o no. Las disminuciones de Jarno y NMTB son consistentes, pero las familias de Jacobs y Morse varían.
Hay adaptadores disponibles para permitir el uso de un tipo de herramienta cónica, p. Morse, en una máquina con un cono diferente, p.e. R8 o viceversa, y adaptadores más simples que consisten en un manguito cónico externo e interno para permitir el uso de una pequeña herramienta Morse en una máquina de mayor diámetro.
Uno de los primeros usos de los conos fue montar brocas directamente en máquinas herramienta, como en el contrapunto de un torno, aunque posteriormente se desarrollaron portabrocas que sujetaban brocas de vástago paralelo.
Marrón y negro Sharpe
Marrón y marrón Los conos Sharpe, estandarizados por la empresa del mismo nombre, son una alternativa al cono Morse más común. Al igual que los Morse, estos tienen una serie de tamaños, del 1 al 18, siendo el 7, 9 y 11 los más comunes. La conicidad real de estos se encuentra dentro de un rango estrecho cercano a 0,500 pulgadas por pie (41,67 mm por metro).
Tamaño | Lg. Dia. | Sm. Dia. | Duración | Taper (in/ft) | Taper (in/in) |
---|---|---|---|---|---|
1 | 0.2392 | 0.2000 | 0.94 | 0,5020 | 0,04183 |
2 | 0.2997 | 0,2500 | 1.19 | 0,5020 | 0,04183 |
3 | 0,353 | 0.3125 | 1.50 | 0,5020 | 0,04183 |
4 | 0.4207 | 0,3500 | 1.69 | 024 | 0,04187 |
5 | 0,5388 | 0.4500 | 2.13 | 016 | 0,04180 |
6 | 0,5996 | 0,5000 | 2.38 | 0,533 | 0,04194 |
7 | 0,7201 | 0.6000 | 2.88 | 0,5010 | 0,04175 |
8 | 0.8987 | 0,7500 | 3.56 | 0,5010 | 0,04175 |
9 | 1.0775 | 0.9001 | 4.25 | 0,509 | 0,04174 |
10 | 1.2597 | 1.0447 | 5.00 | 0,561 | 0,04301 |
11 | 1.4978 | 1.2500 | 5.94 | 0,5010 | 0,04175 |
12 | 1.7968 | 1.5001 | 7.13 | 0.4997 | 0,04164 |
13 | 2.0731 | 1.7501 | 7.75 | 0,502 | 0,04168 |
14 | 2.3438 | 2.0000 | 8.25 | 0,5000 | 0,04167 |
15 | 2.6146 | 2.2500 | 8.75 | 0,5000 | 0,04167 |
16 | 2.8854 | 2.5000 | 9.25 | 0,5000 | 0,04167 |
17 | 3.1563 | 2.7500 | 9.75 | 0,5000 | 0,04167 |
18 | 3.4271 | 3.0000 | 10.25 | 0,5000 | 0,04167 |
Jacobs
El Jacobs Taper (abreviado JT) se usa comúnmente para asegurar los portabrocas del taladro a un eje. Los ángulos cónicos no son consistentes y varían desde 1,41° por lado para el No. 0 (y el oscuro #2+1⁄2) a 2,33° por lado para el n.º 2 (y el n.º 2 corto).
También hay varias tallas entre el nº 2 y el nº 3: nº 2 corta, nº 6 y nº 33.
Taper | Small End | Big End | Duración |
---|---|---|---|
No. 0 | 0.22844 en (5.8024 mm) | 0.2500 en (6.3500 mm) | 0.43750 en (11.113 mm) |
No. 1 | 0.33341 en (8.4686 mm) | 0,3840 en (9,7536 mm) | 0.65625 en (16.669 mm) |
No. 2 | 0.48764 en (12.386 mm) | 0.5590 en (14.199 mm) | 0.87500 en (22.225 mm) |
No. 2 Short | 0.48764 en (12.386 mm) | 0,5488 en (13.940 mm) | 0,75000 en (19,050 mm) |
#2+1.2 | 0.625 en (15.875 mm) | 0.677 en (17.196 mm) | 1.055 en (26.797 mm) |
No. 3 | 0.74610 en (18.951 mm) | 0.8110 en (20.599 mm) | 1.21875 en (30.956 mm) |
No. 4 | 1.0372 en (26.345 mm) | 1.1240 en (28.550 mm) | 1.6563 en (42.070 mm) |
No. 5 | 1.3161 en (33.429 mm) | 1.4130 en (35.890 mm) | 1.8750 en (47.625 mm) |
No. 6 | 0.6241 en (15.852 mm) | 0.6760 en (17.170 mm) | 1.0000 en (25.400 mm) |
No. 33 | 0.5605 en (14.237 mm) | 0,6240 en (15.850 mm) | 1.0000 en (25.400 mm) |
Jarno
Las velas de Jarno utilizan un esquema muy simplificado. La tasa de conicidad es de 1:20 en el diámetro, en otras palabras, 0,600" en diámetro por pie, .050" en diámetro por pulgada. Los conos varían desde el número 2 hasta el número 20. El diámetro del extremo grande en pulgadas es siempre el tamaño del cono dividido por 8, el extremo pequeño es siempre el tamaño del cono dividido por 10 y la longitud es el tamaño del cono dividido por 2. Por ejemplo, un Jarno No. 7 mide 0,875" (7/8) a lo largo del extremo grande. El extremo pequeño mide 0,700" (7/10) y la longitud es de 3,5" (7/2).
El sistema fue inventado por Oscar J. Beale de Brown & Sharpe.
Taper | Gran final | Pequeño final | Duración | Taper/ f | Taper/ dentro | Ángulo desde centro/° |
---|---|---|---|---|---|---|
No. 2 | 0,2500 | 0.2000 | 1.00 | .6000 | 0500 | 1.4321 |
No. 3 | 0,3750 | 0,3000 | 1.50 | .6000 | 0500 | 1.4321 |
No. 4 | 0,5000 | 0,4000 | 2.00 | .6000 | 0500 | 1.4321 |
No. 5 | 0.6250 | 0,5000 | 2.50 | .6000 | 0500 | 1.4321 |
No. 6 | 0,7500 | 0.6000 | 3.00 | .6000 | 0500 | 1.4321 |
No 7 | 0.8750 | 0,7000 | 3.50 | .6000 | 0500 | 1.4321 |
No. 8 | 1.0000 | 0,8000 | 4.00 | .6000 | 0500 | 1.4321 |
No. 9 | 1.1250 | 0,900 | 4.50 | .6000 | 0500 | 1.4321 |
No. 10 | 1.2500 | 1.0000 | 5.00 | .6000 | 0500 | 1.4321 |
No. 11 | 1.3750 | 1.1000 | 5.50 | .6000 | 0500 | 1.4321 |
No. 12 | 1.5000 | 1.2000 | 6.00 | .6000 | 0500 | 1.4321 |
No. 13 | 1.6250 | 1.3000 | 6.50 | .6000 | 0500 | 1.4321 |
No. 14 | 1.7500 | 1.4000 | 7.00 | .6000 | 0500 | 1.4321 |
No. 15 | 1.8750 | 1.5000 | 7.50 | .6000 | 0500 | 1.4321 |
No. 16 | 2.0000 | 1.6000 | 8.00 | .6000 | 0500 | 1.4321 |
No. 17 | 2.1250 | 1.7000 | 8.50 | .6000 | 0500 | 1.4321 |
No. 18 | 2.2500 | 1.8000 | 9.00 | .6000 | 0500 | 1.4321 |
No. 19 | 2.3750 | 1.9000 | 9.50 | .6000 | 0500 | 1.4321 |
No. 20 | 2.5000 | 2.0000 | 10.000,00 | .6000 | 0500 | 1.4321 |
Morse

El cono Morse fue desarrollado por Stephen A. Morse, con sede en New Bedford, Massachusetts, a mediados de la década de 1860. Desde entonces, ha evolucionado para abarcar tamaños cada vez más pequeños y ha sido adoptado como estándar por numerosas organizaciones, incluida la Organización Internacional de Normalización (ISO) como ISO 296 y el Instituto Alemán de Normalización (DIN) como DIN 228-1. Es uno de los tipos más utilizados y es particularmente común en el vástago de brocas helicoidales de vástago cónico y escariadores de máquinas, en los husillos de taladradoras industriales y en los contrapuntos de los tornos. El ángulo de conicidad del cono Morse varía algo según el tamaño, pero suele ser de 1,49 grados (alrededor de 3 grados incluidos).
Algunos implantes totales de cadera ortopédicos modulares utilizan un cono Morse para unir los componentes. De manera similar, algunos implantes dentales utilizan un cono Morse para conectar componentes.
Tamaños
Los conos Morse vienen en ocho tamaños identificados por números enteros entre 0 y 7, y un tamaño medio (4 1/2; se encuentra muy raramente y no se muestra en la tabla). A menudo, la designación se abrevia como MT seguida de un dígito; por ejemplo, un número de cono Morse 4 sería MT4. El cono MT2 es el tamaño que se encuentra con mayor frecuencia en taladradoras de hasta 1⁄2" capacidad. Ocasionalmente se encuentran versiones cortas (cortas), con el mismo ángulo cónico pero un poco más de la mitad de la longitud habitual, para los tamaños de números enteros del 1 al 5. Existen estándares para estos, que, entre otras cosas, a veces se utilizan en cabezales de torno para conservar un orificio pasante del eje más grande.
Tipos de finales
Los conos Morse son del tipo autosujetante y pueden tener tres tipos de extremos:
- tang (lustrado) para facilitar el impulso positivo, evitando el deslizamiento
- roscado para ser sostenido en el lugar con una barra de dibujo
- plana (sin tang o sección roscada)
Los conos autoportantes dependen de una gran preponderancia de carga axial sobre carga radial para transmitir pares elevados. Pueden surgir problemas al utilizar brocas grandes en relación con el vástago, si el orificio piloto es demasiado grande. El estilo roscado es esencial para cualquier carga lateral, en particular el fresado. La única excepción es que estas situaciones desfavorables se pueden simular para eliminar un mango atascado. Permitir la charla ayudará a soltar el agarre. El ángulo de conicidad agudo (estrecho) puede provocar dicho atasco con cargas axiales pesadas o durante períodos prolongados.
Ocasionalmente se ven fresas de extremo con vástago cónico Morse con espiga: por seguridad, deben usarse con un collar en C o similar, encajando en el cuello entre la fresa y el vástago, y tirando hacia atrás contra el extremo grande de el cono
El tapiz en sí es aproximadamente de 5/8" por pie, pero las proporciones exactas y las dimensiones para los diferentes tamaños de los punteros tipo tang se dan a continuación.
Dimensiones

Número de cinta de morse | Taper | A | B (max) | C (max) | D (max) | E (max) | F | G | H | J | K |
---|---|---|---|---|---|---|---|---|---|---|---|
0 | 1:19.212 | 9.045 | 56,5 | 59,5 | 10,5 | 6 | 4 | 1 | 3 | 3.9 | 1° 29' 27" |
1 | 1:20.047 | 12.065 | 62 | 65,5 | 13 | 8.7 | 5 | 1.2 | 3.5 | 5.2 | 1° 25' 43" |
2 | 1:20.020 | 17.780 | 75 | 80 | 16 | 13.5 | 6 | 1.6 | 5 | 6.3 | 1° 25' 50" |
3 | 1:19.922 | 23.825 | 94 | 99 | 20 | 18,5 | 7 | 2 | 5 | 7.9 | 1° 26' 16" |
4 | 1:19.254 | 31.267 | 117,5 | 124 | 24 | 24,5 | 8 | 2.5 | 6.5 | 11.9 | 1° 29' 15" |
5 | 1:19.002 | 44.399 | 149,5 | 156 | 29 | 35,7 | 10 | 3 | 6.5 | 15.9 | 1° 30' 26" |
6 | 1:19.180 | 63.348 | 210 | 218 | 40 | 51 | 13 | 4 | 8 | 19 | 1° 29' 36" |
7 | 1:19.231 | 83.058 | 285.75 | 294.1 | 34.9 | – | – | 19.05 | – | 19 | 1° 29' 22" |
B Tapers
Los conos de la serie B son un estándar DIN (DIN 238) que normalmente se utiliza para colocar mandriles en sus ejes, como la serie de conos Jacobs más antigua. Cada cono de la serie B es efectivamente el extremo pequeño o grande de un cono Morse:
- B10 = pequeño extremo de MT1 (D = 10.095 mm)
- B12 = gran extremo de MT1 (D = 12.065 mm)
- B16 = pequeño extremo de MT2 (D = 15.733 mm)
- B18 = gran extremo de MT2 (D = 17.780 mm)
- B22 = pequeño extremo de MT3 (D = 21.793 mm)
- B24 = extremo grande de MT3 (D = 23.825 mm)
El número después de la B es el diámetro (D) del extremo grande del tapiz a la mm más cercana, y 'aproximadamente' 1mm más grande que el extremo grande de la toma (~2mm en el caso de B22 y B24)
Familia de conos NMTB

La Asociación Nacional de Constructores de Máquinas Herramienta (ahora llamada Asociación para la Tecnología de Fabricación) definió un cono pronunciado que se utiliza comúnmente en las fresadoras. El cono se denomina de diversas formas NMTB, NMT o NT. El cono es de 3.500 pulgadas por pie y también se conoce como "7 en 24" o 24/7; el ángulo calculado es 16,5943 grados. Todas las herramientas NMTB tienen esta conicidad, pero las herramientas vienen en diferentes tamaños: NMTB-10, 15, 20, 25, 30, 35, 40, 45, 50 y 60. Aparentemente, estas conicidades también se especificaron en ASA (ahora ANSI) B5. 10-1943.
NMTB es un grabador "autoliberante" o "rápido". A diferencia de los grifos de autocontención más agudos arriba, tales grifos no están diseñados para transmitir el par alto; los torques altos se llevan por las teclas de conducción ranuras atractivas en la brida. El propósito es permitir un cambio rápido y fácil entre diferentes herramientas (ya sea automáticamente o a mano) asegurando al mismo tiempo que la herramienta o el portaherramienta se conectará de forma estricta y rígida a la husillo, y con precisión coaxial con ella. El extremo más grande adyacente a la herramienta hace más rigidez de lo posible con los grifos Morse o R8 equipados con máquinas comparables.
La patente 1794361 (presentada el 25 de marzo de 1927) describe las formas de herramientas y husillos de fresadoras utilizando un cono pronunciado. La patente fue asignada a Kearney & Trecker Corporation, Brown &Amp; Sharpe y Cincinnati Milling Machine Company. La patente quería un cono que liberara libremente la herramienta y descubrió que un cono de 3,5 en 12 tenía esa propiedad. La patente también utilizaba las chavetas, las ranuras y una cola en el vástago de la herramienta para evitar que el vástago de la herramienta se cayera del husillo de una fresa horizontal mientras el operador conectaba la barra de tiro.
ANSI B5.18-1972 especifica algunas dimensiones esenciales para fresar husillos de máquinas y manivelas de herramientas utilizando tamaños de cinta 30, 40, 45, 50, 60. Las especificaciones describen la posición de la llave de conducción y la brida y el hilo del perno del cajón que sostiene la paja en el husillo.
Las herramientas se denominan Cambio Rápido; Constructores Nacionales de Máquinas Herramienta & #39; Asociación, 1927; NMTB; Cono de máquina estándar americano, ANSI B5.18; DIN 2080 / ES 2340; ISO R 290-2583. Existen ligeras variaciones en roscas y bridas (JIS B 6339: MAS 403); y las normas europeas (por ejemplo, cono ISO) utilizan roscas métricas.
Los mangos de las herramientas NMTB tenían un cono de 7 en 24, pero también tenían una cola de diámetro constante (piloto) en el extremo del mango que se describió en la patente de 1927. Las variaciones de diseño posteriores dejaron caer la cola (acortando el vástago) y colocaron una ranura en V en la brida que ayudó al cambio automático de herramientas. Los diseños modernos comenzaron a utilizar barras de tiro eléctricas que sujetaban pernos de tracción (también conocidos como perillas de retención) que se atornillaban al vástago de la herramienta en lugar de barras de tiro atornilladas. La barra de tiro eléctrica agarraría el perno de tracción en lugar de atornillarse al vástago de la herramienta.
Los diseños de portaherramientas más modernos se conocieron como Caterpillar "V-Flange", CAT, V-Flange, ANSI B5.50, SK, ISO, International (INT), BT, ISO 7388-1. , DIN 69871, NFE 62540. Una vez más existen ligeras variaciones en el utillaje. Aunque las dimensiones cónicas básicas son las mismas, existen diferencias en las bridas, los tamaños de las roscas de entrada y los pernos de tracción; las versiones internacionales utilizan tamaños métricos.
Cono HSK



Los portaherramientas HSK se desarrollaron a principios de los años 90. HSK significa de:Hohlschaftkegel; En alemán, "conos de mango hueco".
Los conos pronunciados tienden a aflojarse a alta velocidad, ya que sus vástagos sólidos son más rígidos que los husillos en los que encajan, por lo que bajo una fuerza centrífuga elevada, el husillo se expande más que el portaherramientas, lo que cambia la longitud total: es decir, a medida que el husillo 'se expande' el portaherramientas tiende a moverse más profundamente en el husillo en el eje z, lo que puede provocar la producción de piezas que están fuera de tolerancia. El vástago hueco de HSK es deliberadamente delgado y flexible, por lo que se expande más que el husillo y se aprieta cuando gira a alta velocidad. Además, el soporte HSK tiene doble contacto: se acopla con el husillo tanto en el cono como en la parte superior de la brida, lo que evita el movimiento axial cuando se produce crecimiento térmico y/o fuerza centrífuga del husillo.
La flexibilidad también se utiliza para proporcionar una ubicación axial precisa. Un portaherramientas HSK tiene un vástago cónico y una brida con una superficie de contacto. El vástago es corto (aproximadamente la mitad de largo que el de otras máquinas), con un cono poco profundo (una proporción de 1:10) y ligeramente demasiado grande para permitir que la brida se asiente completamente en el casquillo. Las paredes delgadas, el mango corto y la forma cónica poco profunda proporcionan una gran abertura en la parte posterior de la herramienta. Un collar de expansión encaja allí y se acopla con un chaflán de 30° dentro del vástago. A medida que la barra de tiro se retrae, expande el collar y empuja el vástago hacia el interior del casquillo, comprimiendo el vástago hasta que la brida se asienta contra la parte delantera del eje. Esto proporciona una conexión rígida y repetible porque utiliza la fuerza centrífuga dentro del husillo. A medida que aumentan las fuerzas centrífugas, el collar de expansión dentro del HSK fuerza a las paredes del vástago del portaherramientas a permanecer en contacto con la pared del husillo.
El diseño HSK se desarrolló como un estándar no propietario. El grupo de trabajo que elaboró el estándar HSK estaba formado por representantes del mundo académico, la Asociación Alemana de Fabricación de Herramientas y un grupo de empresas y usuarios finales internacionales. Los resultados fueron las normas DIN alemanas 69063 para el husillo y 69893 para el mango. El grupo de trabajo HSK no adoptó un diseño de producto específico, sino más bien un conjunto de estándares que definían los portaherramientas HSK para diferentes aplicaciones. El grupo definió en total seis formas de mango HSK, en nueve tamaños.
Los tamaños se identifican por el diámetro de la brida del vástago en milímetros. Estos diámetros se toman de la serie R10′ de números preferidos, de 25 a 160 mm.
Hoy en día, las formas de los vástagos se designan con las letras de la A a la F y T. Las principales diferencias entre las formas son las posiciones de las ranuras de accionamiento, las ranuras de ubicación de las pinzas, los orificios de refrigerante y el área de la brida.
d1 mm | formas | d2 mm | l1 mm | l2 mm | f1 mm | f5 mm | d8 | b1 |
---|---|---|---|---|---|---|---|---|
20 | E | 15.203 | 10 | 2.0 | 8 | - | - | - |
25 | A, C, E | 19.006 | 13 | 2.5 | 10 | - | - | - |
32 | A, C, E | 24.007 | 16 | 3.2 | 20 | 10.0 | 4.0 | 7.05 |
40 | A, C, E | 30.007 | 20 | 4.0 | 20 | 10.0 | 4.6 | 8.05 |
50 | A, C, E | 38.009 | 25 | 5.0 | 26 | 12,5 | 6.0 | 10.54 |
63 | A, C, E | 48.010 | 32 | 6.3 | 26 | 12,5 | 7.5 | 12.54 |
80 | A, C | 60.012 | 40 | 8.0 | 26 | 16.0 | 8,5 | 16.04 |
100 | A, C | 75.013 | 50 | 10.0 | 29 | 16.0 | 12.0 | 20.02 |
125 | A, C | 95.016 | 63 | 12,5 | 29 | - | - | 25.02 |
160 | A, C | 120.016 | 90 | 16.0 | 31 | - | - | 30.02 |
d1 mm | formas | d2 mm | l1 mm | l2 mm | f1 mm | d8 | b1 |
---|---|---|---|---|---|---|---|
25 | - | - | - | - | - | - | - |
32 | - | - | - | - | - | - | - |
40 | B, D | 24.007 | 16 | 3.2 | 20 | 4.0 | 10 |
50 | B, D, F | 30.007 | 20 | 4.0 | 26 | 4.6 | 12 |
63 | B, D, F | 38.009 | 25 | 5.0 | 26 | 6.0 | 16 |
80 | B, D, F | 48.010 | 32 | 6.3 | 26 | 7.5 | 18 |
100 | B, D | 60.012 | 40 | 8.0 | 29 | 8,5 | 20 |
125 | B, D | 75.013 | 50 | 10.0 | 29 | 12.0 | 25 |
160 | B, D | 95.016 | 63 | 12,5 | 31 | 12.0 | 32 |
A es la forma básica. El vástago en forma de B es una variante para aplicaciones de alto torque y tiene una brida de un tamaño más grande en relación con el diámetro de su eje. (Por lo tanto, un vástago A-40 encajará en un casquillo B-50).
Las formas C y D son variantes simplificadas de A y B para uso manual, eliminando características para acomodar cambiadores automáticos de herramientas como una ranura en V y ranuras de orientación asociadas, y un hueco para un chip RFID.
Las bridas y conos de las formas E y F son similares a las formas A y B, pero están diseñadas para mecanizado de muy alta velocidad (20 000 rpm y más) de materiales livianos al eliminar todas las características asimétricas para minimizar el desequilibrio y la vibración.
ASME B5.62 "Herramientas cónicas huecas con contacto de cara de brida" e ISO 12164-3:2014 "Dimensiones de mangos para herramientas estacionarias" incluyen una forma T adicional, que es bidireccionalmente compatible con la forma A, pero tiene una tolerancia mucho más estricta en los anchos de las chavetas y chaveteros utilizados para la alineación angular. Esto permite sujetar con precisión las herramientas de torno no giratorias.
Una conexión HSK depende de una combinación de fuerzas de sujeción axiales y interferencia de corte de cinta. Todas estas fuerzas son generadas y controladas por los parámetros de diseño de los componentes de apareamiento. El manguito y el husillo deben tener exactamente punteros y caras que sean cuadradas al eje del tapiz. Hay varios métodos de sujeción HSK. Todos utilizan algún mecanismo para amplificar la acción de sujeción de segmentos de collets igualmente espaciados. Cuando el portaherramienta se sujeta en la husillo, la fuerza de la barra de tracción produce un contacto firme de metal a metal entre la manivela y el ID de la unidad de sujeción. Una aplicación adicional de la fuerza de barras bloquea positivamente los dos elementos juntos en una articulación con un alto nivel de rigidez radial y axial. A medida que los segmentos de colletes giran, el mecanismo de sujeción gana fuerza centrífuga. El diseño HSK en realidad aprovecha la fuerza centrífuga para aumentar la fuerza conjunta. La fuerza centrífuga también hace que las paredes delgadas de la manada se desvíen radialmente a un ritmo más rápido que las paredes del husillo. Esto contribuye a una conexión segura garantizando un fuerte contacto entre la manivela y la husillo. Las industrias automotrices y aeroespaciales son los mayores usuarios de las herramientas HSK. Otra industria que está viendo un uso creciente es la industria del molde y la de la muerte.
R8
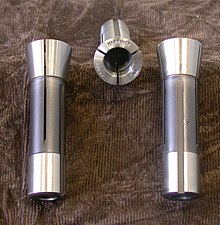
Este grabador fue diseñado por Bridgeport Machines, Inc. para su uso en sus máquinas de fresado. Los grifos R8 no son autosuficientes, por lo que requieren un cajón que se extiende a través de la husillo a la parte superior de la máquina para evitar el desatar cuando se encuentran fuerzas laterales. También son claves (ver imagen) para prevenir la rotación durante la inserción y la eliminación, aunque es el tapiz que transmite el par en uso. El hilo de barra es típicamente 7.16′′–20 tpi (UNF). El ángulo del cono es 16°51′ (16.85°) con un OD de 1.25′ y una longitud de 15.16′. (fuente, Bridgeport Fabricante) El diámetro de la porción de localización paralela no es un tamaño "fraccional" como las otras dimensiones y es 0.949′′′ a 0.9495′′′.
Las herramientas con cono R8 se insertan directamente en el husillo de la máquina. Las pinzas R8 se utilizan normalmente para sujetar herramientas con vástagos redondos, aunque se puede sujetar cualquier forma si la pinza tiene la forma correspondiente cortada. Las pinzas tienen un orificio de precisión con ranuras de compresión axial para sujetar herramientas de corte y están roscadas para la barra de tiro. El sistema R8 se usa comúnmente con pinzas que varían en tamaño desde 1⁄8″ a 3⁄4″ de diámetro o portaherramientas con el Diámetros iguales o ligeramente mayores. Las pinzas o portaherramientas se colocan directamente en el husillo y la barra de tiro se aprieta en la parte superior de la pinza o portaherramientas desde arriba del husillo. Otras herramientas, como portabrocas, cortadores de mosca, cortadores de plaquitas indexables, etc., pueden tener un vástago cónico R8 incorporado o agregado a la herramienta.
El cono R8 se encuentra comúnmente en Bridgeport y molinos de torre similares de EE. UU., o en copias (muy comunes) de estos molinos de otros lugares. La popularidad se debe en gran parte al éxito de Bridgeport y otras fábricas que siguieron el modelo de ella y se produjeron durante gran parte del siglo XX.
Contenido relacionado
Historia de la cámara
Tubo de vacío
Señales de humo