LEDs
A light-emitting diode or led (also known by the acronym LED, from English light-emitting diode ) is a light source made of a semiconductor material with two terminals. This is a p-n junction diode, which emits light when on. If a suitable voltage is applied to the terminals, electrons recombine with holes in the p-n junction region of the device, releasing energy in the form of photons. This effect is called electroluminescence, and the color of the generated light (which depends on the energy of the emitted photons) is determined by the width of the semiconductor's bandgap. LEDs are typically small (less than 1mm²) and some optical components are associated with them to form a radiation pattern.
The first LEDs were manufactured as electronic components for practical use in 1962 and emitted low-intensity infrared light. These infrared LEDs continue to be used as transmitter elements in remote control circuits, such as remote controls used within a wide variety of consumer electronics products. Early visible light LEDs were also low intensity and limited to the red spectrum. Modern LEDs can span wavelengths within the visible, ultraviolet, and infrared spectrums, and achieve very high luminosities.
Early LEDs were used in electronic equipment as indicator lamps to replace incandescent bulbs. They soon became associated for numeric displays in the form of seven-segment alphanumeric displays, at the same time they were incorporated into digital watches. Recent developments already allow the use of LEDs for ambient lighting in its different applications. LEDs have enabled the development of new display screens and sensors, and their high switching speeds allow them to be used for advanced communications technologies as well.
Today, LEDs offer many advantages over conventional incandescent or fluorescent light sources, including lower power consumption, longer lifespan, improved physical robustness, smaller size, and manufacturability. in many different colors of the visible spectrum in a much more defined and controlled way; in the case of multicolored LEDs, with a fast switching frequency.
These diodes are now used in applications so varied that they cover all current technological areas, from Bioengineering, Medicine and Health, going through nanotechnology and quantum computing, electronic devices or lighting in engineering of Mines; Among the most popular are the backlighting of TV and computer screens, as well as mobile devices, the navigation light of airplanes, the headlights of vehicles, advertisements, lighting in general, traffic lights, lamps of sparkles and luminous wall papers. As of the beginning of 2017, LED lamps for home lighting are as cheap or cheaper than compact fluorescent lamps with similar behavior to LEDs. They are also more energy efficient and possibly less of a problem to dispose of as waste. environmental.
History
Discovery and early devices
The phenomenon of electroluminescence was discovered in 1907 by British experimenter Henry Joseph Round of Marconi Laboratories using a silicon carbide crystal and a cat's whisker detector. Soviet inventor Oleg Losev reported the Construction of the first LED in 1927. His research appeared in Soviet, German, and British scientific journals, but the discovery was not put into practice until several decades later. Kurt Lehovec, Carl Accardo and Edward Jamgochian interpreted the mechanism of these first led diodes in 1951, using a device that used silicon carbide crystals, with a pulse generator and a current power supply, and in 1953 with a variant crystal clear.
Rubin Braunstein of RCA reported in 1955 on the infrared emission from gallium arsenide (GaAs) and other semiconductor alloys. Braunstein observed that this emission was generated in diodes constructed from gallium antimonide (GaSb), gallium arsenide (GaAs), indium phosphide (InP), and silicon germanium (SiGe) alloys at room temperature and 77 kelvins.
In 1957, Braunstein also demonstrated that these rudimentary devices could be used for non-radio communication over short distances. As Kroemer points out, Braunstein set up a very simple line of optical communications: he took music coming from a record player and processed it using suitable electronics to modulate the direct current produced by a GaAs Gallium Arsenide diode. The light emitted by the GaAS diode was able to sensitize a PbS Lead Sulfide diode located at a certain distance. The signal thus generated by the PbS diode was fed into an audio amplifier and transmitted through a loudspeaker. When the light beam was intercepted between the two LEDs, the music stopped. This setup already foreshadowed the use of LEDs for optical communications.
In September 1961, James R. Biard and Gary Pittman, working at Texas Instruments (TI) in Dallas, Texas, discovered infrared radiation (900 nm) coming from a tunnel diode they had built using a substrate of gallium arsenide (GaAs). In October 1961 they demonstrated the existence of efficient light emissions and signal coupling between the light-emitting gallium arsenide p-n junction and an electrically isolated photodetector constructed of a semiconductor material. Based on their discoveries, on August 8, 1962 Biard and Pittman produced a patent titled "Semiconductor Radiant Diode" which described how a zinc alloy diffused during the growth of the crystal that forms the substrate of a p-n led junction with a cathode contact far enough apart, allowed the emission of infrared light efficiently in forward bias.
In view of the importance of their investigations, as they appeared in their engineering notebooks and even before communicating their results coming from the laboratories of General Electric, Radio Corporation of America, IBM, Bell Laboratories or those of the Lincoln Laboratory of the Massachusetts Institute of Technology, they were granted a patent by the United States Patent and Trademark Office for the invention of gallium arsenide infrared light-emitting diodes (US patent US3293513A), which are considered as the first LEDs in practical use. Immediately after the patent was filed, TI started a project to manufacture the infrared diodes. In October 1962, Texas Instruments developed the first commercial LED (the SNX-100), which used a pure gallium arsenide crystal for 890 nm light emission. In October 1963, TI released the first commercial hemispherical LED, the SNX-110.
The first LED with emission in the visible spectrum (red) was developed in 1962 by Nick Holonyak.Jr when he worked at General Electric. Holonyak submitted a report in Applied Physics Letters on December 1, 1962. In 1972 M. George Craford, Holonyak's undergraduate student, invented the first yellow LED and improved the luminosity of red and red-orange LEDs. by a factor of ten. In 1976, T. P. Pearsall built the first high-brightness, high-efficiency LEDs for telecommunications over fiber optics. For this he discovered new semiconductor materials expressly adapted to the wavelengths of the aforementioned transmission by optical fibers.
Initial Business Development
Early commercial LEDs were generally used to replace incandescent lamps and neon indicator lamps as well as seven-segment displays. First in expensive equipment such as electronic and laboratory test equipment, and later in other electrical devices such as televisions, radios, telephones, calculators, as well as wristwatches. Until 1968, visible and infrared LEDs were extremely expensive, on the order of $200 per unit, and therefore of little practical use. The Monsanto Company was the first to mass-produce visible LEDs, using gallium arsenide phosphide. (GaAsP) in 1968 to produce red LEDs for indicators.
Hewlett-Packard (HP) introduced LEDs in 1968, initially using GaAsP supplied by Monsanto. These red LEDs were bright enough to be used as indicators, since the light emitted was not enough to illuminate an area. The readings on the calculators were so faint that plastic lenses were placed over each digit to make them readable. Later, other colors appeared that were widely used in gadgets and equipment. In the 1970s Fairchild Optoelectronics commercially successfully manufactured LED devices for less than five cents each. These devices used composite semiconductor chips fabricated using the planar process invented by Fairchild Semiconductor's Jean Hoerni. Planar processing for chip fabrication combined with innovative potting methods enabled the team led by optoelectronics pioneer Thomas Brandt to achieve the necessary cost reductions at Fairchild. These methods continue to be used by LED manufacturers.
Most LEDs were manufactured in typical T1¾ 5mm and T1 3mm packages, but with increasing power output it has become increasingly necessary to remove excess heat to maintain reliability Therefore, it has been necessary to design more complex encapsulations designed to achieve efficient heat dissipation. The packages currently used for high-power LEDs bear little resemblance to those of early LEDs.
Blue LED
Blue LEDs were first developed by RCA's Henry Paul Maruska in 1972 using Gallium Nitride (GaN) on a sapphire substrate. The SiC type (made of silicon carbide) began to be commercialized by Cree, Inc., United States in 1989. However, none of these blue LEDs was very bright.
The first high-brightness blue LED was introduced by Shuji Nakamura of the Nichia Corp. in 1994 starting from the material Gallium-Indium Nitride (InGaN). Isamu Akasaki and Hiroshi Amano in Nagoya were working in parallel, on the nucleation Gallium Nitride on sapphire substrates, thus obtaining p-type doping with said material. As a result of their research, Nakamura, Akasaki and Amano were awarded the Nobel Prize in Physics. In 1995, Alberto Barbieri of the Cardiff University (UK) laboratory was investigating the efficiency and reliability of high-brightness LEDs and how As a result of the investigation, he obtained a LED with a transparent contact electrode using indium tin oxide (ITO) on aluminum-gallium-indium phosphide and gallium arsenide.
In 2001 and 2002 processes were carried out to grow gallium nitride LEDs on silicon. As a consequence of these investigations, in January 2012 Osram launched high-power LEDs made of gallium-indium nitride grown on a silicon substrate.
White LED and evolution
The achievement of high efficiency in blue LEDs was quickly followed by the development of the first white LED. In such a device a coating “phosphor” (fluorescent material) Y3 Al5 O12:Ce (known as YAG or yttrium garnet and aluminum) absorbs some of the blue emission and generates yellow light by fluorescence. Similarly it is possible to introduce other "phosphors" that generate green or red light by fluorescence. The resulting mixture of red, green, and blue is perceived by the human eye as white; on the other hand, it would not be possible to appreciate red or green objects by illuminating them with the YAG phosphor since it generates only yellow light together with a remnant of blue light.
Early white LEDs were expensive and inefficient. However, the intensity of light produced by LEDs has increased exponentially, with a doubling time occurring approximately every 36 months since the 1960s (according to Moore's Law). This trend is generally attributed to a parallel development of other semiconductor technologies and advances in optics and materials science, and has come to be called Haitz's law after Roland Haitz.
The light output and efficiency of blue and near-UV LEDs increased as the cost of lighting fixtures made from them decreased, leading to the use of white-light LEDs for illumination. The fact is that they are replacing incandescent and fluorescent lighting.
White LEDs can produce 300 lumens per electrical watt while lasting up to 100,000 hours. Compared to incandescent bulbs this means not only a huge increase in electrical efficiency but also a similar or lower cost per bulb.
Principle of operation
A P-N junction can provide an electrical current when illuminated. Similarly, a P-N junction traversed by a direct current can emit light photons. These are two ways of considering the phenomenon of electroluminescence. In the second case, this could be defined as the emission of light by a semiconductor when it is subjected to an electric field. The charge carriers recombine in a forward-biased P-N junction. Specifically, the electrons from the N region cross the potential barrier and recombine with the holes from the P region. The free electrons are in the conduction band while the holes are in the valence band. In this way, the energy level of the holes is lower than that of the electrons. When electrons and holes recombine, a fraction of the energy is emitted in the form of heat and another fraction in the form of light.
The physical phenomenon that takes place in a PN junction when the current passes in direct bias, therefore, consists of a succession of electron-hole recombinations. The phenomenon of recombination is accompanied by the emission of energy. In ordinary Germanium or Silicon diodes, phonons or vibrations of the crystalline structure of the semiconductor are produced, which simply contribute to its heating. In the case of LED diodes, the semiconductor materials are different from the previous ones, being, for example, various type III-V alloys such as gallium arsenide (AsGa), gallium phosphide (PGa) or phosphoarsenide of gallium (PAsGa).
In these semiconductors, the recombinations that take place at the PN junctions remove excess energy by emitting light photons. The color of the emitted light depends directly on its wavelength and is characteristic of each specific alloy. Currently, alloys are manufactured that produce light photons with wavelengths in a wide range of the electromagnetic spectrum within the visible, near infrared and near ultraviolet. What is achieved with these materials is to modify the width in energies of the forbidden band, thus modifying the wavelength of the emitted photon. If the LED diode is reverse polarized, the recombination phenomenon will not occur, so it will not emit light. Reverse bias can damage the diode.
The electrical behavior of the led diode in forward bias is as follows. If the polarization voltage increases, from a certain value (which depends on the type of semiconductor material), the LED begins to emit photons, the ignition voltage has been reached. Electrons can be moved across the junction by applying different voltages to the electrodes; Thus the emission of photons begins and as the polarization voltage increases, the intensity of light emitted increases. This increase in light intensity is coupled with the increase in current intensity and can be diminished by Auger recombination. During the recombination process, the electron jumps from the conduction band to the valence band, emitting a photon and accessing, by conservation of energy and momentum, a lower energy level, below the Fermi level of the material. The emission process is called radiative recombination, which corresponds to the phenomenon of spontaneous emission. Thus, in each electron-hole radiative recombination, a photon of energy equal to the width in energies of the forbidden band is emitted:
Eg=hf=hcλ λ {displaystyle E_{g}=hf={frac {hc}{lambda }qquad }where c is the speed of light and f and λ are the frequency and wavelength, respectively, of the light it emits. This description of the foundation of the emission of electromagnetic radiation by the LED diode can be seen in the figure where a schematic representation of the PN junction of the semiconductor material is made together with the energy diagram, involved in the process of recombination and light emission., at the bottom of the drawing. The wavelength of the emitted light, and therefore its color, depends on the width of the band gap of energy. The most important substrates available for light emission applications are GaAs and InP. LED diodes can decrease their efficiency if their spectral absorption and emission peaks as a function of their wavelength are very close, as is the case with GaAs:Zn (zinc-doped gallium arsenide) LEDs, since part of the light that They emit and absorb it internally.
The materials used for LEDs have a forward-biased bandgap whose width in energies ranges from infrared, visible, or even near-ultraviolet light. The evolution of LEDs began with gallium arsenide red and infrared devices. Advances in materials science have made it possible to manufacture devices with increasingly shorter wavelengths, emitting light in a wide range of colors. LEDs are generally fabricated on an N-type substrate, with an electrode connected to the P-type layer deposited on its surface. P-type substrates, although less common, are also manufactured.
Technology
Physical Foundation
A led begins to emit when a voltage of 2-3 volts is applied to it. In reverse bias, a different vertical axis is used than in forward bias to show that the absorbed current is practically constant with the voltage until breakdown occurs.
The led is a diode formed by a semiconductor chip doped with impurities that create a PN junction. As in other diodes, current flows easily from the p, or anode, side to the n, or cathode side, but not in the opposite direction. Charge carriers (electrons and holes) flow to the junction from two electrodes placed at different voltages. When an electron recombines with a hole, its energy level drops, and the excess energy is released as a photon. The wavelength of the emitted light, and therefore the color of the LED, depends on the width in energy of the forbidden band corresponding to the materials that constitute the pn junction.
In silicon or germanium diodes, electrons and holes recombine generating a non-radiative transition, which does not produce any light emission since they are semiconductor materials with an indirect band gap. The materials used in the LEDs have a direct band gap with an energy width that corresponds to the near-infrared (800 nm - 2500 nm), visible and near-ultraviolet (200-400 nm) light spectrum. The development of LEDs began with red and infrared light devices made of gallium arsenide (GaAs). Advances in materials science have made it possible to build devices with ever smaller wavelengths, emitting light within a wide range of colors.
LEDs are typically fabricated from an n-type substrate, with one of the electrodes attached to the p-type layer deposited on its surface. p-type substrates are also used, although they are less common. Many commercial LEDs, especially GaN/InGaN LEDs, also use sapphire (aluminum oxide) as a substrate.
Most of the semiconductor materials used in the manufacture of LEDs have a very high refractive index. This implies that most of the light emitted inside the semiconductor is reflected when it reaches the outer surface that is in contact with the air by a phenomenon of total internal reflection. The extraction of light is, therefore, a very important aspect that is in constant research and development to take into consideration in the production of LEDs.
Index of refraction

Most of the semiconductor materials used in the manufacture of LEDs have a very high refractive index with respect to air. This implies that most of the light emitted inside the semiconductor will be reflected when it reaches the outer surface that is in contact with the air by a phenomenon of total internal reflection.
This phenomenon affects both the light emission efficiency of LEDs and the light absorption efficiency of photovoltaic cells. The refractive index of silicon is 3.96 (at 590 nm), while that of air is 1.0002926. The extraction of light is, therefore, a very important aspect in constant research and development to take into consideration. in the production of LEDs.
In general, an uncoated flat-surface LED semiconductor chip will emit light only in the direction perpendicular to the semiconductor surface and in very close directions, forming a cone called a light cone or escape cone. The maximum The angle of incidence that allows photons to escape from the semiconductor is known as the critical angle. When this angle is exceeded, photons no longer escape from the semiconductor but are instead reflected within the semiconductor crystal as if there were a mirror on the outer surface.
Due to internal reflection, light that has been reflected internally from one face can escape through other crystal faces if the angle of incidence now becomes low enough and the crystal is transparent enough not to reflect the emission back of photons inward. However, in a simple cubic led with external surfaces at 90 degrees, all faces act as equal angled mirrors. In this case, most of the light cannot escape and is lost as heat within the semiconductor crystal.
A chip with angled facets on its surface similar to those of a cut jewel or a Fresnel lens can increase light output by allowing light to be emitted in orientations that are perpendicular to the usually more numerous outer facets of the chip than the only six of a cubic sample.
The ideal shape of a semiconductor to obtain the maximum output of light would be that of a microsphere with the emission of photons located exactly in the center of it, and equipped with electrodes that penetrate to the center to connect with the point broadcast. All light rays from the center would be perpendicular to the surface of the sphere, which would result in no internal reflections. A hemispherical semiconductor would also work correctly since the flat part would act as a mirror to reflect the photons so that all light could be emitted entirely through the hemisphere.
Transitional coverings
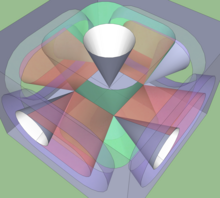
After a wafer of semiconductor material is built, it is cut into small pieces. Each fragment is called a chip and becomes the small active part of a light-emitting LED diode.
Many LED semiconductor chips are encapsulated or embedded inside molded plastic casings. The plastic casing is intended to achieve three purposes:
- Facilitate the assembly of the semiconductor chip on lighting devices.
- Protect from physical damage to the fragile electrical wiring associated with the diode.
- Acting as an intermediary element for the refraction between the high rate of semiconductor and air.
The third characteristic contributes to increase the emission of light from the semiconductor by acting as a diffusing lens, allowing the light to be emitted to the outside with an angle of incidence on the outer wall much greater than that of the narrow cone of light coming from the uncoated chip.
Efficiency and operational parameters
LEDs are designed to operate with an electrical power of no more than 30-60 milliwatts (mW). Around 1999, Philips Lumileds introduced more powerful LEDs capable of running continuously at one watt power. These LEDs used much larger semiconductor dies in order to accept higher power supplies. In addition, they were mounted on metal rods to facilitate heat removal.
One of the main advantages of LED-based lighting sources is their high luminous efficiency. White LEDs quickly matched and even exceeded the efficiency of standard incandescent lighting systems. In 2002, Lumileds manufactured five-watt LEDs, with a luminous efficiency of 18-22 lumens per watt (lm/W). For comparison, a conventional 60-100 watt incandescent bulb puts out around 15 lm/W, and standard fluorescent lamps put out up to 100 lm/W.
As of 2012, Future Lighting Solutions had achieved the following efficiencies for some colors. Efficiency values show the light power output for each watt of electrical power input. The luminous efficiency values include the characteristics of the human eye and have been derived from the luminosity function.
Color | Wave length (nm) | Efficiency ratio | Luminous efficacy (Lm/W) | |
---|---|---|---|---|
Red | 620 ” λ 645 | 0.39 | 72 | |
Orange red | 610 ” λ 620 | 0.29 | 98 | |
Green | 520 ” λ 550 | 0.15 | 93 | |
Cian | 490 ” λ 520 | 0.26 | 75 | |
Blue | 460 ” λ 490 | 0.35 | 37 |
In September 2003, Cree Inc. manufactured a new type of blue LED that drew 24 milliwatts (mW) at 20 milliamps (mA). This enabled a new white light packaging that produced 65lm/W at 20 milliamps, making it the brightest white LED available on the market; it also turned out to be more than four times more efficient than standard incandescent bulbs. In 2006 they presented a white LED prototype with a record luminous efficiency of 131 lm/W for a current of 20 milliamps. Nichia Corporation has developed a white LED with a luminous efficiency of 150 lm/W and a forward current of 20 mA. Cree Inc.'s LEDs, called xlamp xm-L, came on the market in 2011, producing 100 lm/W at the maximum power of 10 W, and up to 160 lm/W with an electrical input power of about 2 W. In 2012, Cree Inc. introduced a white LED capable of producing 254 lm/W, and 303 lm/W at March 2014. General lighting needs in practice require high power LEDs, one watt or more. They work with currents greater than 350 milliamps.
These efficiencies refer to the light emitted by the diode kept at a low temperature in the laboratory. Since LEDs, once installed, operate at high temperatures and with conduction losses, the efficiency is actually much lower. The United States Department of Energy (DOE) has carried out tests to replace incandescent lamps or CFLs with LED lamps, showing that the average efficiency achieved is about 46 lm/W in 2009 (the behavior during the tests remained the same). in a range of 17 lm/W to 79 lm/W).
Loss of efficiency
When the electrical current supplied to a LED exceeds a few tens of milliamps, the luminous efficiency decreases due to an effect called loss of efficiency.
At first, an explanation was sought attributing it to high temperatures. However, the scientists were able to show the opposite, that while the life of the LED may be shortened, the drop in efficiency is less severe at elevated temperatures. In 2007, the cause of the drop in efficiency was attributed to Auger recombination. which gives rise to a mixed reaction. Finally, a 2013 study definitively confirmed this theory to justify the loss of efficiency.
In addition to reducing efficiency, LEDs that work with higher electrical currents generate more heat, which compromises the life of the LED. Due to this increase in heat at high currents, high brightness LEDs have an industry standard value of only 350 mA, a current for which there is a balance between brightness, efficiency and durability.
Possible solutions
Given the need to increase the luminosity of the LEDs, this is not achieved by increasing the current levels but by using several LEDs in a single lamp. Therefore, solving the problem of the loss of efficiency of domestic LED lamps consists of using the fewest possible number of LEDs in each lamp, which contributes to significantly reducing costs.
Members of the United States Naval Research Laboratory have found a way to slow the drop in efficiency. They discovered that this drop comes from the non-radiative Auger recombination produced with the injected carriers. To solve this, they created quantum wells with a soft confinement potential to slow non-radiative Auger processes.
Researchers at National Taiwan Central University and Epistar Corp are developing a method to decrease efficiency loss by using aluminum nitride ceramic substrates, which have higher thermal conductivity than commercially used sapphire. Heating effects are reduced due to the high thermal conductivity of the new substrates.
Half-life and failure analysis
Solid-state devices such as LEDs have very limited obsolescence if operated at low currents and low temperatures. Life times are 25,000 to 100,000 hours, but the influence of heat and current can increase or decrease this time significantly.
The most common failure of LEDs (and laser diodes) is gradual reduction in light output and loss of efficiency. The first red LEDs stood out for their short life. With the development of high power LEDs, devices are subjected to higher junction temperatures and higher current densities than traditional devices. This places stress on the material and can cause early degradation of light output. To quantitatively classify the useful life in a standardized way, it has been suggested to use the parameters L70 or L50, which represent the life times (expressed in thousands of hours) in which a given LED reaches 70% and 50% of the initial light emission, respectively.
Just as in most previous light sources (incandescent lamps, discharge lamps, and those that burn fuel, for example candles and oil lamps) light was generated by a thermal process, LEDs they only work properly if they are kept cool enough. The manufacturer typically specifies a maximum junction temperature between 125 and 150 °C, and lower temperatures are recommended in the interest of achieving long life for the LEDs. At these temperatures, relatively little heat is lost by radiation, which means that the light beam generated by an LED is considered cold.
The residual heat in a high-power LED (which as of 2015 can be considered less than half the electrical power it consumes) is transported by conduction through the substrate and encapsulation to a heat sink, which removes heat in the environment by convection. It is therefore essential to carry out a careful thermal design, taking into account the thermal resistances of the encapsulation of the LED, the heat sink and the interface between them. Medium power LEDs are typically designed to be soldered directly to a printed circuit board that has a thermally conductive metal layer. High-power LEDs are encapsulated in large-area ceramic packages designed to be attached to a metallic heat sink, the interface being a material of high thermal conductivity (thermal paste, phase change material, conductive thermal pad, or hot melt glue).).
If an LED fixture is installed in a light fixture with no ventilation, or the environment lacks fresh air circulation, the LEDs are likely to overheat, shortening their lifespan or even leading to anticipated deterioration of the light fixture. Thermal design is typically projected for an ambient temperature of 25°C (77°F). LEDs used in outdoor applications, such as traffic signals or pavement marking lights, and in climates where the temperature inside the lighting fixture is very high, can experience anywhere from a reduction in light output to a complete failure.
Since the efficiency of LEDs is higher at low temperatures, this technology is ideal for lighting supermarket freezers. Because LEDs produce less residual heat than incandescent lamps, their use in freezers can also save refrigeration costs. However, they can be more susceptible to frost and frost buildup than incandescent lamps, so some LED lighting systems have been fitted with a heating circuit. In addition, heat sink techniques have been developed so that they can transfer the heat produced at the junction to parts of lighting equipment that may be of interest.
Colours and materials
Conventional LEDs are made from a variety of inorganic semiconductor materials. The following table shows the colors available with their range of wavelengths, differences in working potential and materials used.
Color | Onda Longitude [nm] | Potential difference [ΔV] | Semiconductor material | |
---|---|---|---|---|
Infrared radiation | λ 760 | ΔV 1.63 | Arseniuro de Galio (GaAs) Arseniuro de galio-aluminio (AlGaAs) | |
Red | 610 ” λ 760 | 1.63 ΔV 2.03 | Arseniuro de galio-aluminio (AlGaAs) Fosfuro de galio y arsenic (GaAsP) Fosfuro de aluminum-galio-indio (AlGaInP) Fosfato de galio (GaP) | |
Orange | 590 ” λ 610 | 2.03 ΔV 2.10 | Fosfuro de galio y arsenic (GaAsP) Fosfuro de aluminum-galio-indio (AlGaInP) Fosfato de galio (GaP) | |
Yellow | 570; λ 590 | 2.10 ΔV 2.18 | Fosfuro de galio y arsenic (GaAsP) Fosfuro de aluminum-galio-indio (AlGaInP) Fosfato de galio (GaP) | |
Green | 500 ” λ 570 | 1.9 ΔV. 4.0 | Classic green: Fosfato de galio (GaP) Fosfuro de aluminum-galio-indio (AlGaInP) Fosfuro de galio-aluminio (AlGaP) Pure green: Gallio-Indian nitride (InGaN) / Gallium nitride (GaN) | |
Blue | 450 ” λ 500 | 2.48 ΔV 3.7 | Zinc Selenide (ZnSe) Nitruro de galio-indio (InGaN) Silicon carbide (SiC) as substrate Silicon (Si) as a substrate (in development) | |
Violeta | 400 ” λ. 450 | 2.76 ΔV. 4.0 | Nitruro de galio-indio (InGaN) | |
Purple | Combination of different types | 2.48 ΔV 3.7 | Blue/red dual ledes, blue with red phosphorus, or white with purple plastic. | |
Ultraviolet | λ 400 | 3 ΔV. 4.1 | Nitruro de galio-indio (InGaN) (385-400 nm)
Diamond (C) (235 nm) | |
Rosa | Combination of different types | ΔV ~ 3.3 | Blue with one or two layers of phosphorus, yellow with red, orange or pink phosphorus, white with pink plastic, or white phosphorus with pink dye above. | |
White | Wide spectrum | 2.8 ΔV. 4.2 | Pure White: Blue or UV Led with yellow phosphorus Warm white: Blue led with orange phosphorus. |
Blue and ultraviolet
The first blue-violet LED used chlorine doped with magnesium and was developed by Herb Maruska and Wally Rhines at Stanford University in 1972, PhD students in materials science and engineering. At the time Maruska was working on the RCA Laboratories, where he collaborated with Jacques Pankove. In 1971, a year after Maruska left for Stanford, his RCA colleagues Pankove and Ed Miller demonstrated the first blue electroluminescence from gallium nitride-doped zinc; however the device Pankove and Miller built, the first real gallium nitride light-emitting diode, did emit green light. In 1974 the US Patent Office granted Maruska, Rhines, and Stanford professor David Stevenson a patent (patent US3819974 A) from his 1972 work on the doping of gallium nitride with magnesium which today remains the basis of all commercial blue LEDs and laser diodes. These devices built in the 1970s did not have sufficient light output for practical use, so research into gallium nitride diodes slowed down. In August 1989 Cree introduced the first commercial blue LED with an indirect transition across the bandgap in a silicon carbide (SiC) semiconductor. SiC LEDs have a very low luminous efficiency, no better than 0. 03%, but they emit in the visible blue region.
In the late 1980s, breakthroughs in epitaxial growth and p-type doping on GaN ushered in the modern era of GaN optoelectronic devices. Based on this, Theodore Moustakas patented a blue LED production method at Boston University using a novel two-step process. Two years later, in 1993, high-intensity blue LEDs were taken up by Shuji Nakamura of the Nichia Corporation using GaN synthesis processes similar to Moustakas's. Moustakas and Nakamura were assigned separate patents, leading to legal conflicts between Nichia and Boston University (not least because, despite Moustakas inventing his process first, Nakamura registered his earlier). This new development revolutionized LED lighting, making high-power blue light sources more cost-effective, leading to the development of technologies like Blu-ray, and enabling bright, high-resolution displays. of modern tablets and phones.
Nakamura was awarded the Millennium Technology Prize for his contribution to high-power LED technology and high performance. He was also awarded, along with Hiroshi Amano and Isamu Akasaki, the Nobel Prize in Physics in 2014 for their decisive contribution to high-performance LEDs and blue LEDs. In 2015, a US court ruled that three companies (that is, the same plaintiff companies that had not previously resolved their disputes) and that they had the patents de Nakamura for US production, had infringed Moustakas' previous patent and ordered them to pay a license fee worth $13 million.
At the end of the 90s, blue LEDs were already available. These feature an active region consisting of one or more InGaN quantum wells sandwiched between thicker sheets of GaN, called pods. By varying the In/Ga fraction in InGaN quantum wells, the light emission can theoretically be changed from violet to amber. Aluminum gallium nitride AlGaN with a variable content of the Al/Ga fraction can be used to make the sheath and sheets of quantum wells for ultraviolet diodes, but these devices have not yet reached the level of efficiency and technological maturity of blue/green InGaN/GaN devices. If GaN is used undoped, the device emits near-ultraviolet light with a peak centered at a wavelength around 365 nm to form the active layers of the quantum wells. Green LEDs manufactured in the InGaN/GaN mode are much more efficient and brighter than LEDs produced with nitride-free systems, but these devices are still too low in efficiency for high-brightness applications.
Using aluminum nitrides, such as AlGaN and AlGaInN, even shorter wavelengths are achieved. A range of UV LEDs for different wavelengths are becoming available on the market. Near-UV emitting LEDs with wavelengths around 375-395 nm are already cheap enough and readily available, for example to replace black light lamps in UV anti-counterfeit watermark inspection on some documents and paper money. Diodes with shorter wavelengths (up to 240 nm) are currently on the market, although they are noticeably more expensive.
As the photosensitivity of microorganisms approximately coincides with the absorption spectrum of DNA (with a peak around 260 nm), it is expected to use UV LEDs with emission in the region of 250-270 nm in disinfection equipment and sterilization. Recent research has shown that commercially available UV LEDs (365 nm) are effective in disinfection and sterilization devices. UV-C wavelengths were obtained in laboratories using aluminum nitride (210 nm), aluminum nitride boron (215 nm) and diamond (235 nm).
RGB

RGB LEDs consist of a red, a blue and a green LED. By independently adjusting each of them, RGB LEDs are capable of producing a wide range of colors. Unlike dedicated single color LEDs, RGB LEDs do not produce pure wavelengths. Also, commercially available modules are often not optimized for smooth color mixing.
RGB systems
RGB systems
There are two basic ways to produce white light. One is to use individual LEDs that emit the three primary colors (red, green, and blue) and then mix the colors together to form white light. The other way is to use a phosphor to convert the monochromatic light from a blue or UV LED into a broad spectrum of white light. It is important to note that the whiteness of the light produced is essentially designed to satisfy the human eye and depending on each case it may not always be appropriate to think of it as strictly white light. The wide variety of whites that are achieved with fluorescent tubes serve as a point of reference.
There are three main methods of producing white light with LEDs.
- Led blue + green LED + red led (color mixing; although it can be used as background light for screens) for lighting are very poor due to the empty intervals in the frequency spectrum.
- Led UV nearby or UV + RGB phosphorus (a LED light that generates a shorter wavelength than blue is used to excite a RGB phosphorus).
- Blue led + yellow phosphorus (two complementary colors are combined to produce white light; it is more efficient than the first two methods and therefore is more used in practice).
Due to metamerism, it is possible to have different spectra that appear white. However, the appearance of objects illuminated by that light can change as the spectrum changes. This optical phenomenon is known as color run, it is different from color temperature, and it makes a truly orange or cyan object appear to be another color and much darker as the LED or associated phosphor do not emit those wavelengths.. The best color rendering with CFLs and LEDs is achieved by using a mix of phosphors, which provides lower efficiency but better light quality. Although the highest color temperature halogen is orange, it is still the best available artificial light source in terms of color rendering.
White light can be produced by adding lights of different colors; the most common method is the use of red, green, and blue (RGB). Hence the method is called multicolor white LEDs (sometimes known as RGB LEDs). Because they require electronic circuitry to control the mixing and diffusion of the different colors, and because the individual colored LEDs have slightly different emission patterns (leading to color variation depending on the viewing direction), even if they are made in a single unit, they are rarely used to produce white light. However, this method has many applications due to its flexibility in producing color mixing and, in principle, for offering greater quantum efficiency in the production of white light.
There are several types of multicolor white LEDs: di-tri- and tetrachromatic white LEDs. Several key factors influence these different realizations, such as color stability, natural color rendering index and luminous efficiency. Frequently, a higher luminous efficiency will imply a less naturalness of the color, thus creating a trade-off between the luminous efficiency and the naturalness of the colors. For example, dichromatic white LEDs have the best luminous efficiency (120 lm/W), but the lowest color rendering ability. On the other hand, tetrachromatic white LEDs offer excellent color rendering capabilities but are often accompanied by poor luminous efficiency. Trichromatic white LEDs are in an intermediate position, have good luminous efficiency (>70 lm/W) and reasonable color rendering capability.
One of the challenges pending to be solved consists in the development of more efficient green LEDs. The theoretical maximum for green LEDs is 683 lumens per watt, but as of 2010 only a few green LEDs exceeded 100 lumens per watt. The blue and red LEDs, however, are approaching their theoretical limits.
Multicolor LEDs offer the possibility not only to produce white light but also to generate lights of different colors. Most of the perceptible colors can be formed by mixing different proportions of the three primary colors. This allows precise dynamic control of color. As more research effort is devoted to the multicolor LED method, it is becoming more influential as the fundamental method used to produce and control the color of light.
Although this type of LED can play a good role in the market, some technical problems must be solved first. For example, the emission power of these LEDs decreases exponentially with increasing temperature, producing a substantial change in color stability. These problems may make it impossible for them to be employed in the industry. For this reason, many new encapsulation designs have been carried out and their results are under study by researchers. Of course, multicolor LEDs without phosphors can never provide good illumination because each one emits a very narrow band of color. While phosphorless LEDs are a very poor lighting solution, they offer the best solution for LCD backlit displays or direct lighting with LED pixels.
In LED technology, the decrease in the correlated color temperature (CCT) is a reality that is difficult to avoid because, together with the useful life and the effects of the temperature variation of the LEDs, it ends up modifying the final real color of the same. To correct this, feedback loop systems are used, provided, for example, with color sensors to monitor, control and maintain the color resulting from the superposition of monocolor LEDs.
Phosphor-based LEDs
This method involves coating LEDs of one color (mainly blue InGaN LEDs) with phosphors of different colors to produce white light; the resulting combination LEDs are called phosphor-based white LEDs or white LEDs with a phosphor converter (PCLED). A fraction of blue light undergoes the Stokes shift that transforms shorter wavelengths into longer wavelengths. Depending on the color of the original led, phosphors of different colors can be used. Applying several layers of differently colored phosphors broadens the emission spectrum, effectively increasing the Color Rendering Index (CRI) value of a given LED.
Efficiency losses of phosphor-based LEDs (with fluorescent substances) are due to heat losses generated by the Stokes shift and also due to other degradation issues related to such fluorescent substances. Compared to normal LEDs their luminous efficiencies depend on the spectral distribution of the resulting light output and the original wavelength of the LED itself. For example, the luminous efficiency of a yellow YAG phosphor typical of a white led is 3 to 5 times the luminous efficiency of the original blue led, due to the higher sensitivity of the human eye for the yellow color than for the blue color (depending on the model of the brightness function). Due to its simplicity of manufacture, the phosphor (fluorescent material) method remains the most popular for achieving high intensity white LEDs. The design and production of a light source or lamp using a monochromatic emitter with fluorescent phosphor conversion is simpler and cheaper than a complex RGB system, and most high intensity white LEDs on the market today are They are manufactured using the conversion of light by fluorescence.
Among the challenges that arise to improve the efficiency of LED-based white light sources is the development of more efficient fluorescent substances (phosphors). As of 2010, the most efficient yellow phosphor continues to be YAG phosphor, which has a Stokes shift loss of less than 10%. Internal optical losses due to reabsorption in the LED chip itself and in the LED encapsulation constitute 10% to 30% of the efficiency loss. Currently, in the field of phosphor development, a great effort is devoted to its optimization in order to achieve greater light production and higher operating temperatures. For example, efficiency can be increased by better potting design or by using a more suitable type of phosphor. The trim coating process is often used in order to be able to regulate the variable thickness of the phosphor.
Some white phosphor-coated LEDs consist of blue InGaN LEDs encapsulated in an epoxy resin coated with a phosphor. Another option is to associate the LED with a separate phosphor, a prefabricated piece of polycarbonate that is preformed and coated with the phosphor material. Separate phosphors provide more diffuse light, which is favorable for many applications. Separate phosphor designs are also more tolerant of variations in the LED emission spectrum. A very common yellow phosphor material is cerium-doped aluminum yttrium aluminum garnet (Ce 3+:YAG).
White LEDs can also be made with near-ultraviolet (NUV) LEDs coated with a mixture of high-efficiency europium phosphors that emit red and blue, plus aluminum-copper-doped zinc sulfide (ZnS:Cu, Al) which emits green. This procedure is analogous to the operation of fluorescent lamps. The procedure is less efficient than blue LEDs with YAG:Ce phosphor, since the Stokes shift is more important, so a greater fraction of the energy is converted to heat, still generating light with better spectral characteristics and, therefore, with better color reproduction.
Since UV LEDs have a higher output radiation than blue LEDs, both methods ultimately provide similar brightness. A drawback of the latter is that possible leakage of UV light from a malfunctioning light source can cause damage to human eyes or skin.
Other white LEDs
Another method used to produce white light experimental LEDs without the use of phosphors is based on the growth epitaxy of zinc selenide (ZnSe) on a ZnSe substrate that simultaneously emits blue light from its active region and yellow light from the substrate.
A new way to produce white LEDs is to use wafers composed of gallium nitride on silicon from 200mm silicon wafers. This avoids the costly fabrication of sapphire substrates from wafers of relatively small sizes, i.e. 100 or 150mm. The sapphire apparatus must be attached to a mirror-like collector to reflect light, which would otherwise be lost. It is predicted that by 2020, 40% of all GaN LEDs will be made on silicon. Manufacturing large sapphire is difficult, while large silicon material is cheap and more abundant. On the other hand, manufacturers of LEDs that switch from sapphire to silicon must make a minimal investment.
Organic LEDs (OLED)
In an organic light-emitting diode (OLED), the electroluminescent material that makes up the emitting layer of the diode is an organic compound. Organic material is conductive due to electronic delocalization of the pi bonds caused by the conjugated system in all or part of the molecule; consequently the material functions as an organic semiconductor. Organic materials can be small organic molecules in the crystalline phase, or polymers.
One of the advantages made possible by OLEDs is thin, low-cost displays with low power supply voltage, a wide viewing angle, high contrast, and a wide color gamut. Polymer LEDs have the added benefit of making displays flexible and printable. OLEDs have been used in the manufacture of visual displays for portable electronic devices such as mobile phones, digital cameras and MP3 players, and possible future uses are also expected to include lighting and television.
Quantum Dot LEDs
At the beginning of the 60s, a decade of technological revolution began with the birth of the Internet and the discovery of LEDs in the visible spectrum. In 1959 the Nobel laureate in physics Richard P. Feynman, in his famous lecture given at the annual meeting of the American Physical Association titled: "There is plenty of room at the bottom: an invitation to enter a new field of physics", already anticipated the technological revolution and the important discoveries that could involve the manipulation of materials until they were reduced to atomic or molecular sizes or scales. But it was not until the following decade of the 1970s that the knowledge of numerous applications of quantum mechanics (about 70 years after its invention) together with advances in growth techniques and synthesis of materials, come to mean an important change in the lines of research of numerous groups.
Already in this decade, the ability to design structures having new optical and electronic properties was combined with the search for new technological applications to materials already existing in nature. In fact, in 1969, L. Esaki et al. proposed the implementation of heterostructures formed by very thin layers of different materials, giving rise to what is known as engineering and design of energy bands in semiconductor materials. The most basic small-dimensional heterostructure is the quantum well (Quantum Well, QW). It consists of a thin layer of a certain semiconductor, of the order of 100 Å, confined between two layers of another semiconductor material characterized by a greater width of the forbidden energy band (bandgap, BG). Due to the small dimensions of the potential well associated with this structure, the carriers see their movement restricted to a plane perpendicular to the direction of growth. Laser diodes with QWs in the active zone had great advantages, such as the ability to select the emission wavelength based on the width of the well or the reduction of the threshold current, the latter related to the density of resulting states. of confinement in a plane.
Others followed naturally from all these advances, such as the study of systems with three-dimensional confinement, that is, quantum dots (QDs). Thus, QDs can be defined as artificial systems of very small size, from a few tens of nanometers to a few microns, in which the carriers are confined in the three directions of three-dimensional space (hence it is called zero-dimensional), in a region of space smaller than its de Broglie wavelength.
When the size of the semiconductor material that constitutes the quantum dot is within the nanometric scale, this material presents a behavior that differs from that observed for it on a macroscopic scale or for the individual atoms that make it up. The electrons in the nanomaterial are restricted to move in a very small region of space and are said to be confined. When this region is so small that it is comparable to the wavelength associated with the electron (the de Broglie length), then what is called quantum behavior begins to be observed. In these systems, their physical properties are not explained by classical concepts but are explained by quantum mechanical concepts. For example, the minimum potential energy of an electron confined within a nanoparticle is higher than expected in classical physics and the energy levels of its different electronic states are discrete. Due to quantum confinement, the size of the particle has a fundamental effect on the density of electronic states and therefore on its optical response. Quantum confinement occurs when the size of the particles has been reduced to approximately the radius of the Bohr exciton (generating an electron-hole pair or exciton in the semiconductor material), remaining confined in a very small space. As a consequence, the structure of the energy levels and the optical and electrical properties of the material are considerably modified. The energy levels become discrete and finite, and strongly depend on the size of the nanoparticle.
They are usually made of semiconductor material and can hold anywhere from none to several thousand electrons. Electrons inside the quantum dot repel each other, it costs energy to introduce additional electrons, and they obey the Pauli exclusion principle, which prohibits two electrons from occupying the same quantum state simultaneously. Consequently, the electrons in a quantum dot form orbits in much the same way as atoms and are in some cases called artificial atoms. They also exhibit electronic and optical behaviors similar to atoms. Its application can be very diverse, in addition to optoelectronics and optics, in quantum computing, in information storage for traditional computers, in biology and in medicine.
The quantum confinement and optical properties of the quantum dot allow its emission color to be adjustable from visible to infrared. Quantum dot LEDs can produce almost all colors in the CIE diagram. In addition, they provide more color options and a better color representation than the white LEDs discussed in the previous sections, since the emission spectrum is much narrower, which is characteristic of confined quantum states.
There are two procedures for excitation of QDs. One uses photoexcitation with a primary LED light source (blue or UV LEDs are commonly used for this). The other procedure uses direct electrical excitation first demonstrated by Alivisatos et al.
An example of the photoexcitation procedure is the one developed by Michael Bowers, at Vanderbilt University in Nashville, making a prototype that consisted of coating a blue led with quantum dots that emitted white light in response to the blue light from the led. The modified LED emitted a warm, yellowish-white light similar to that of incandescent lamps. Research began in 2009 with light-emitting diodes using QD in applications to liquid crystal display (LCD) televisions.
In February 2011 scientists at PlasmaChem GmbH were able to synthesize quantum dots for LED applications by making a light converter that could efficiently transform blue light into light of any other color for many hundreds of hours. Quantum cells can also be used to emit visible or near-infrared light by exciting them with light of a shorter wavelength.
The structure of the quantum dot LEDs (QD-LEDs) used for the electrical excitation of the material, have a basic design similar to that of OLEDs. A layer of quantum dots is located between two layers of a material capable of transporting electrons and holes. By applying an electric field, electrons and holes move towards the quantum dot shell and recombine to form excitons; each exciton produces an electron-hole pair, emitting light. This scheme is the one usually considered for quantum dot displays. The big difference with OLEDs lies in their very small size and as a consequence, they generate the effects and optical properties of quantum confinement.
QDs are also very useful as excitation sources for producing fluorescence images due to the narrow range of wavelengths emitted by the QD manifested in the narrow bandwidth of the peak in the emission spectrum (property due to quantum confinement). For this reason, the use of quantum dot LEDs (QD-LEDs) in the near-field optical microscopy technique has been shown to be efficient.
Regarding energy efficiency, in February 2008 warm light emission with a luminous efficiency of 300 lumens of visible light per watt of radiation (not per electrical watt) was achieved through the use of nanocrystals.
Types
LEDs come in a wide variety of shapes and sizes. The color of the plastic lens usually matches that of the light emitted by the LED, although this is not always the case. For example, purple colored plastic is used for infrared LEDs and most blue LEDs have colorless pots. Modern high power LEDs such as those used for downlighting or backlighting typically appear in surface mount technology (SMT).
Thumbnail
Miniature LEDs are often used as indicators. In through-hole technology and surface mounts their size ranges from 2mm to 8mm. They do not normally have a separate heat sink. The maximum current is between 1mA and 20mA. Its small size constitutes a limitation for the purposes of the power consumed due to its high power density and the absence of a heatsink. They are often daisy chained together to form led light strips.
The most typical plastic roof shapes are round, flat, triangular, and square with a flat top. The encapsulation can also be transparent or colored in order to improve contrast and viewing angles.
Researchers at the University of Washington have invented the thinnest LED. It is made up of two-dimensional (2-D) materials. Its width is 3 atoms, which is 10 to 20 times thinner than three-dimensional (3-D) LEDs and 10,000 times thinner than a human hair. These 2-D LEDs will enable smaller, more energy-efficient nano lasers and optical communications.
There are three main categories of single color miniature LEDs:
- Low Current Intensity
Prepared for a current of 2mA with about 2V (consumption of more or less 4 mW).
- Intermediate or Common Range
- Ledes of 20mA (between 40mW and 90mW) around:
- 1,9 -2,1 V for red, yellow orange and traditional green.
- 3.0-3.4 V for pure and blue green.
- 2.9-4.2 V for violet, rose, purple and white.
- High Current Intensity
For a current of 20mA and with 2 or 4-5 V, designed to be able to see with direct sunlight. The 5V and 12V LEDs are standard miniature LEDs that incorporate a series resistor for direct connection to either 5V or 12V power.
High Power
See also: Solid State Lighting, LED Lamp, High Power LEDs or HP-LED
High-power LEDs (HP-LEDs) or HO-LEDs (High-Output LEDs) can be driven with currents from hundreds of mA to over 1 Ampere, while others LEDs only reach tens of milliAmps. Some can emit over a thousand lumens.
Power densities of up to 300 W/(cm²) have also been achieved. As overheating of the LEDs can destroy them, they have to be mounted on a heatsink. If the heat from an HP-LED was not transferred to the medium, the fixture would fail within a few seconds. An HP-LED can replace an incandescent bulb in a flashlight or several of them can be combined to form a power led lamp. Some well known HP-LEDs in this category are Nichia 19 series, Lumileds Rebel Led, Osram Opto Semiconductors Golden Dragon and Cree X-Lamp. As of September 2009, there are LEDs manufactured by Cree that exceed 105 lm/W.
Examples of Haitz's law, which predicts an exponential increase over time in the light emission and efficiency of a LED, are those of the CREE XP-GE series, which reached 105 lm/W in 2009 and the Nichia 19 series with an average efficiency of 140 lm/W which was released in 2010.
Powered by alternating current
Semiconductor Seoul has developed LEDs that can be powered by alternating current without the need for a DC converter. In one half cycle, one part of the led emits light and the other part is dark, and this happens the other way around during the next half cycle. The normal efficiency of this type of HP-LED is 40 lm/W. A large number of LED elements in series can work directly with mains voltage. In 2009, Seoul Semiconductor released a high voltage led, called 'Acrich MJT', capable of being driven by AC via a simple control circuit. The low power dissipated by these LEDs gives them greater flexibility than other original AC LED designs.
Applications. Variants
Of intermittent flashes
The flashing LEDs are used as attention indicators without the need for any external electronics. Flashing LEDs look similar to standard LEDs, but contain a built-in multi-vibrator circuit that causes the LEDs to flash with a characteristic period of one second. On LEDs fitted with a diffusion lens, this circuit is visible (a small black dot). Most flashing LEDs emit light in a single color, but more sophisticated fixtures can flash multiple colors and even fade through a sequence of colors from RGB color mixing.
Bicolor
Bi-color LEDs contain two different LEDs in a single assembly. There are two types; The first consists of two dies connected to two conductors parallel to each other with current flowing in opposite directions. Current flowing in one direction emits one color and current flowing in the opposite direction emits the other color. In the second type, instead, the two dies have separate terminals and there is a terminal for each cathode or for each anode, so that they can be controlled independently. The most common color combination is traditional red/green, however other combinations are available such as traditional green/amber, pure red/green, red/blue, or pure blue/green.
Tricolors
Tri-color LEDs contain three different emitter LEDs in a single frame. Each emitter is connected to a separate terminal so that it can be controlled independently of the others. An arrangement in which four terminals appear is very characteristic, a common terminal (the three anodes or the three cathodes joined) plus an additional terminal for each color.
RGB
RGB LEDs are tri-color LEDs with red, green, and blue emitters, typically using a four-wire connection and a common terminal (anode or cathode). This type of LEDs can present as common both the positive terminal and the negative terminal. Other models, however, only have two terminals (positive and negative) and a small built-in electronic control unit.
Decorative multicolors
This type of LEDs has emitters of different colors and are equipped with two unique output terminals. The colors are switched internally by varying the supply voltage.
Alphanumeric
Alphanumeric LEDs are available as seven segment displays, fourteen segment displays, or dot matrix displays. Seven-segment displays can display all numbers and a limited set of letters while fourteen-segment displays can display all letters. Dot matrix displays typically use 5x7 pixels per character. The use of seven-segment LEDs became widespread in the 1970s and 1980s, but the increasing use of liquid crystal displays has reduced the popularity of numeric and alphanumeric LEDs due to their lower power requirement and greater display flexibility.
Digital RGB
They are RGB LEDs that contain their own "intelligent" control electronics. In addition to power and ground, they have connections for data input and output, and sometimes for clock or strobe signals. They are connected in a daisy chain, with the data input to the first led equipped with a microprocessor that can control the brightness and color of each one, independently of the others. They are used where a combination is needed to provide maximum control and minimal view of the electronics, such as Christmas string lights or LED arrays. Some even feature refresh rates in the kHz range, making them suitable for basic video applications.
Filaments
An LED filament consists of several LED chips connected in series on a longitudinal substrate forming a thin bar reminiscent of the incandescent filament of a traditional light bulb. Filaments are being used as a low-cost decorative alternative to traditional light bulbs that they are being phased out in many countries. The filaments require a fairly high supply voltage to illuminate with normal brightness, being able to work efficiently and easily at mains voltages. Often a simple rectifier and capacitive current limiter are used as a low cost replacement for the traditional incandescent bulb without the inconvenience of having to build a high current, low voltage converter as required by individual LED diodes. They are typically mounted inside an airtight enclosure that is shaped similar to the lamps they replace (bulb-shaped, for example) and filled with an inert gas such as nitrogen or carbon dioxide to remove the heat efficiently. The main types of LEDs are: miniature, high power devices and common designs such as alphanumeric or multicolor.
Use considerations
Power supplies
Main article: Circuit with LEDs
The characteristic current-voltage curve of an LED is similar to that of other diodes, in which the current intensity (or briefly, current) increases exponentially with the voltage (see Shockley's equation). This means that a small change in voltage can cause a large change in current. If the applied voltage exceeds the LED's forward bias threshold voltage drop, by a small amount, the current limit that the diode can withstand It can be greatly exceeded, being able to damage or destroy the LED. The solution that can be adopted to avoid this consists in using constant current intensity power supplies (constant current source for short) capable of keeping the current below the maximum value of the current that can pass through the led or, therefore, less, if a conventional constant voltage source or battery is used, add a limiting resistor in series with the Led in the LED lighting circuit. Since normal power sources (batteries, mains) are usually constant voltage sources, most LED fixtures must include a power converter or at least a current limiting resistor. However, the high resistance of three-volt button cells combined with the high differential resistance of nitride-derived LEDs makes it possible to power such LEDs from a button cell without the need for an external resistor.
Electrical polarity
Main article: Electrical polarity of LEDs
As with all diodes, current flows easily from p-type material to n-type material. However, if a small voltage is applied in the reverse direction, current does not flow and no light is emitted. If the reverse voltage grows high enough to exceed the breakdown voltage, high current flows and the LED may be damaged. If the reverse current is limited enough to prevent damage, the reverse conduction led can be used as an avalanche diode.
Health and safety
The vast majority of devices containing LEDs are "safe under normal use," and are therefore classified as "Risk Product 1 RG1 (Low Risk)" / "LED Class 1". At present, only a few LEDs - extremely bright LEDs that have a very small viewing angle of 8° aperture or less - could, in theory, cause temporary blindness and are therefore classified as & #34;Risk 2 RG2 (moderate risk)". The opinion of the French Agency for Food Safety, Environment and Occupational Health and Safety (ANSES) when addressing health issues related to LEDs in 2010, suggested prohibiting the public use of lamps that were in Group 2 or Moderate Risk, especially those with a high blue component, in places frequented by children.
In general, safety regulations in the use of laser light —and Risk 1, Risk 2 devices, etc.— are also applicable to LEDs.
Just as LEDs have the advantage over fluorescent lamps that they do not contain mercury, however, they may contain other dangerous metals such as lead and arsenic. Regarding the toxicity of LEDs when treated as waste, a study published in 2011 stated: "According to federal regulations, LEDs are not hazardous, except for low-intensity red LEDs, as they initially of its commercialization contained Pb (lead) in concentrations above the regulatory limits (186 mg/L; regulatory limit: 5). However, in accordance with California regulations, excessive levels of copper (up to 3,892 mg/kg; limit: 2,500), lead (up to 8,103 mg/kg, limit: 1,000), nickel (up to 4,797 mg/kg, limit: 2000), or silver (up to 721 mg/kg, limit: 500) cause all LEDs except low intensity yellow LEDs to be dangerous ".
Advantages
- Efficiency: LEDs emit more lumens per watt than incandescent bulbs. The efficiency of the LED lighting devices is not affected by the shape and size of these in contrast to the fluorescent bulbs or tubes.
- Color: LEDs can emit light of any color, without using any color filters like those needed in traditional lighting methods. This property provides them with greater efficiency and reduces costs.
- Size: LEDs can be very small (less than 2 mm2) and therefore can be easily connected to plates of printed circuits.
- Heating time: the LEDs light very quickly. A typical red led indicator will reach the maximum brightness in less than a microsecond. LEDs used on communications devices can present even shorter response times.
- Cycles: LEDs are ideal in the applications subject to frequent ignition and off cycles, unlike the incandescent and fluorescent lamps that fail when used in this option, or like high discharge intensity lamps (HID lamps) that require a lot of waiting time before restarting the ignition.
- Darkness: LEDs can be easily darkened by modulation by pulse width or by decrease of the direct current. The modulation of the width of the pulses is the reason why the led lights, in particular the car headlights seem to be blinking when viewed through a camera or by some people. It's a case of stroboscopic effect.
- Cold light: Unlike most light sources, LEDs radiate very little heat in the form of infrared radiation which can damage sensitive objects or tissues. The lost energy disappears in the form of heat at the LED base.
- Slowly.: most of the LEDs are slowly damaged over time, unlike the incandescent bulbs that deteriorate abruptly.
- Useful life: LEDs can have a relatively long service life. A report estimates that between 35,000 and 50,000 hours of useful life, although the time normally elapsed until the product ceases to function completely is usually greater. Fluorescent tubes have an estimated useful life of 10,000 to 15 000 hours, depending in part on the conditions of use, and incandescent bulbs of 1000 to 2000 hours. Several manifestations of theDOE have shown that more than energy savings, the reduction of maintenance costs during this extended service life, is the main factor for determining the period of recovery of the investment for a led product.
- Strike resistance: LEDs are solid state components and are therefore difficult to damage with external shocks, unlike the fluorescent and incandescent lamps, which are fragile.
- Approach: a LED system can be designed to focus the light. Incandescent and fluorescent sources often require an external reflector to collect the light and direct it in an appropriate way. In larger LED systems, total internal reflection lenses (TIR) are usually used to achieve the same effect. However, when large amounts of light are needed, many light sources are often deployed, which are difficult to focus or collide to the same place.
Disadvantages
- Initial price: LEDs are currently a bit more expensive (price for lumen) than other lighting technologies. In March 2014, a manufacturer claimed to have already reached the price of one dollar per kilolumen. The additional expenditure comes in part from a relatively low light emission, the drive circuits and the power supply required.
- Temperature Unit: LED performance depends to a large extent on the ambient temperature of the environment, or the procedures used for thermal management. The overload of a led in a high temperature environment can result in overheating of the set of the leds, and a failure of the lighting device. It is necessary to use a suitable heat sink to ensure a long service life. This is especially important in automotive, medical and military applications where devices should operate within a wide range of temperatures, and with low error rates. Toshiba has manufactured LEDs with an operating temperature margin of -40 to 100 °C, which adapts both to facilitate their use in indoors and outdoors and in applications such as lamps, ceiling lights, street lights and light bulbs.
- Sensitivity with tension: LEDs must be supplied to work with a voltage superior to their threshold voltage and with a current below their nominal value. Both the current and the useful life change significantly with a small change in the applied tension. Therefore, they require a regulated supply current (usually enough a series resistance for LED indicators).
- Color reproduction: most cold white LEDs have spectra that differ significantly from the black body irradiation spectrum such as the Sun or an incandescent lamp. The peak at 460nm and the depression at 500nm can make the color of the objects perceived differently under the lighting of a cold white LED that under sunlight or incandescent light sources, due to metamerism. Cold white LEDs based on matches reproduce especially the red surfaces.
- Area associated with the light source: individual LEDs do not approach a punctual light source that provides a spherical light distribution, but rather a lambertian distribution. The leds are applied with difficulty to cases where spherical light fields are needed, however, the luminous fields can be manipulated by applying different optical or “lentes” procedures. LEDs cannot provide divergences below a few degrees. On the contrary, lasers can emit beams with differences of 0.2 degrees or less.
- Electrical polarity: Unlike the incandescent bulbs, which are illuminated independently of the electric polarity, the LEDs will only be lit using the correct electric polarity. To automatically adjust the polarity of the power supply of the led devices, rectifiers can be used.
- Blue danger: There is concern that blue leds and cold white leds are able to overcome the security limits established by the so-called blue light hazard as defined in the eye safety specifications as the IEC 62471.
- Light pollution outdoors: white LEDs, especially those with a high color temperature, emit light of wavelength much shorter than conventional outdoor light sources, such as high pressure sodium steam lamps. On the other hand, we must also take into account the greater sensitivity of our vision to the blue and the green in the scotopic vision and, therefore, shifted in the visible spectrum to 'cold' colors, thus falseing the appreciation of the 'cálidos' colors (made orange and red). As a result, the white LEDs used in outdoor illuminations cause, in a scotopic vision, more night glow in the sky and thus generate more light pollution. The American Medical Association warned about the use of high-blue white LEDs in public lighting, due to their greater impact on human health and the environment, compared to low-blue light sources (e.g., those of High Pressure Sodium, amber leds of computers and low-temperature LEDs.
- Decrease in efficiency: LED efficiency decreases as the electric current increases. Warming also increases with the highest currents, which compromises the useful life of the leds. These effects impose practical limits on LED current values in high-power applications.
- Impact on insects: LEDs are much more attractive to insects than sodium steam lights, which has created a concern for the possibility of causing a disturbance of their food networks.
- Use in winter conditions: Since the leds do not emit much heat compared to the incandescent lamps, the led lights used for traffic control can stay covered in snow what darkens them, and can lead to accidents.
Applications
Indicators and Signal Lamps
The low power consumption, low maintenance, and small size of LEDs have led to their use as status indicators and displays in a wide variety of equipment and installations. Large area led screens are used for game broadcasting in stadiums, as dynamic decorative displays, and as dynamic message signs on highways. The thin, lightweight message displays are used at airports and railway stations and as destination information panels on trains, buses, trams and ferries.
Single color lights are suitable for traffic lights, traffic signals, exit signs, vehicle emergency lighting, navigation lights, headlights (standard chromaticity and luminance indices were established in the International Convention for the Prevention of Collisions at Sea of 1972 Annex 1 and by the International Commission on Illumination or CIE) and Christmas lights made up of LEDs. In regions with cold climates, LED traffic lights can remain covered with snow. Red or yellow LEDs are used in indicators and alphanumeric displays, in environments where night vision must be maintained: aircraft cockpits, submarine and ship bridges, astronomical observatories and in the field for example for the observation of animals during the night and military applications of the field.
Given their long lifespan, fast switching times, and ability to be seen in broad daylight due to their high intensity and concentration, LEDs have been used for car, truck brake lights for some time. and buses, and on direction change signals; Many vehicles now use LEDs in their tail light assemblies. The use in the brakes improves safety due to the great reduction in the time required for a complete ignition, that is to say, due to the fact of presenting a shorter rise time, up to 0.5 seconds faster than an incandescent bulb. This provides more reaction time for drivers behind. In a two-intensity circuit (tail and brake lights) if the LEDs are not driven with a fast enough frequency, they can create a ghost matrix, where the LED ghosts will appear if the eyes move quickly across the light arrangement.. Headlights equipped with white LEDs are beginning to be used. The use of LEDs has stylistic advantages because they can form much narrower beams than incandescent lamps with parabolic reflectors.
Low power LEDs are relatively inexpensive and allow for use in short-lived luminous objects such as illuminated stickers, disposable objects, and Lumalive photonic fabric. Artists also use LEDs for so-called LED art. The weather and distress radio receivers with coded area messages (SAME) have three LEDs: red for alarms, orange for attention and yellow for warnings, indications and reports.
Lighting
To encourage the switch to LED lighting, the US Department of Energy has created the L Award. The Philips Lighting North America LED bulb won first award on August 3, 2011 after successfully completing 18 months of intensive field, laboratory and product testing.
LEDs are used as street lights and in architectural lighting. Mechanical robustness and long lifespan are used in automotive lighting on cars, motorcycles, and bicycle lights. LED light emission can be effectively controlled through the use of non-imaging optical principles.
In 2007, the Italian town of Torraca was the first place to convert its entire lighting system to LED. LEDs are also used in aviation, Airbus has used LED lighting on its Airbus A320 since 2007, and Boeing uses led lighting on the 787. LEDs are now also used in airport and heliport lighting. LED airport fixtures currently include medium intensity runway lights, runway centerline lights, taxiway centerline lights, and edge lights.
LEDs are also used as a light source for DLP projectors and to illuminate LCD televisions (known as LED TVs) and laptop screens. RGB LEDs raise the color gamut by up to 45%. TV screens and computer screens can be made thinner by using LEDs for backlighting. The lack of infrared or thermal radiation makes LEDs ideal for stage lighting with banks of RGB LEDs that can easily change color and decrease heating lighting, as well as medical lighting where IR radiation can be harmful. In energy conservation, there is less heat production when using LEDs.
In addition, they are small, durable and require little power, which is why they are used in portable devices such as flashlights. Led strobes or camera flashes operate at a safe, low voltage, rather than the 250+ volts commonly found in xenon flash based lighting. This is especially useful for mobile phone cameras. LEDs are used for infrared illumination in night vision applications including security cameras. A ring of LEDs around a forward-facing video camera on a retroreflective background enables chroma coding in video productions.
LEDs are used in mining operations, as cap lamps to provide light for miners. Research has been done to improve mining LEDs, reduce glare and increase illumination, reducing the risk of injury to miners.
LEDs are now commonly used in all market areas, from commercial to domestic use: standard lighting, theatrical, architectural, public facilities, and wherever artificial light is used.
LEDs are finding more and more uses in medical and educational applications, for example as mood enhancement, and new technologies such as AmBX, exploiting the versatility of LED. NASA has even sponsored research for the use of LEDs to promote health for astronauts.
Optical communications. Data Transfer and Other Communications
Light can be used to transmit data and analog signals. For example, white LEDs can be used in systems to help people orient themselves in enclosed spaces in order to locate arrangements or objects.
Asistive listening devices in many theaters and similar venues use arrays of infrared LEDs to send sound to the audience's receivers. LEDs (and also semiconductor lasers) are used to send data over many types of fiber optic cable. From TOSLINK cables for digital audio transmission to the very high-bandwidth fiber links that make up the backbone of the Internet. For some time computers were equipped with IrDA interfaces, which allowed them to send and receive data from nearby equipment using infrared radiation.
Because LEDs can turn on and off millions of times per second, they require very high bandwidth for data transmission.
Sustainable lighting
Lighting efficiency is necessary for sustainable architecture. In 2009, tests carried out with LED bulbs by the United States Department of Energy showed an average efficiency from 35 lm/W, therefore below the efficiency of CFLs, to values as low as 9 lm/W, worse than incandescent bulbs. A typical 13-watt LED bulb put out 450 to 650 lumens, which was equivalent to a standard 40-watt incandescent bulb.
In any case, in 2011 there were LED bulbs with an efficiency of 150 lm/W, and even low-end models exceeded 50 lm/W, so a 6-watt LED could achieve the same results. than a standard 40-watt incandescent bulb. The latter have a durability of 1000 hours while a LED can continue to operate at a lower efficiency for more than 50,000 hours.
Comparative table of led-CFL-incandescent bulb:
Led | CFL | Incandescent bulb | |
---|---|---|---|
Life | 50,000 hours | 10,000 | 1,200 hours |
Watts by bulb | 10 | 14 | 60 |
Pissed by light bulb | $2.00 | $7.00 | $1.25 |
kW consumed in 50,000 hours | 500 | 700 | 3000 |
Electrical Cost ($0.10/kW) | $50. | $70 | $300 |
Bulbs required to complete 50,000 hours of light | 1 | 5 | 42 |
Bulb gas for 50,000 hours of light | $2.00 | $35.00 | $52.50 |
Total cost for 50,000 hours of light | $52.00 | $105.00 | $352.50 |
Power consumption
The reduction in electrical energy consumption achieved with LED-based lighting is significant when compared to incandescent lighting. In addition, this reduction is also manifested as a notable decrease in damage to the environment. Each country presents a different energy panorama and, therefore, although the impact on energy consumption is the same, the production of gases that are harmful to the environment may fluctuate somewhat from one country to another. Regarding consumption, a conventional 40-watt incandescent bulb can be taken as a sample. An equivalent light output can be obtained with a 6-watt LED system. Using, then, the LED system instead of incandescent bulbs, energy consumption can be reduced by more than 85%. Regarding the saving in environmental impact, it is possible to quantify it for any country if the production of CO2 per kW per hour is known. In the specific case of Spain, it is known that the energy mix of the Spanish electricity grid has produced about 308 g of CO2/kWh in 2016. It is assumed for the calculation that both the bulb and the LED assembly They have worked for 10 hours a day throughout the year 2016. The energy consumed has been 146 kW-hour by the incandescent bulb and 21.6 kW-hour by the LED set. The electrical energy consumed can be translated into kg of CO2 produced per year. In the first case, the generation of about 45 kg of CO2 has been carried out, while in the second case the production of CO2 has been reduced to 6.75 kg.
Light sources for artificial vision systems
Industrial vision systems usually require homogeneous lighting to be able to focus on features of the image of interest. This is one of the most frequent uses of LED lights, and it will surely continue to be so, lowering the prices of systems based on light signaling. Barcode scanners are the most common example of vision systems, many of these low-cost products use LEDs instead of lasers. Optical computer mice also use LEDs for their vision system, as they provide a source of uniform light on the surface for the miniature camera inside the mouse. In fact, LEDs are a nearly ideal light source for vision systems for the following reasons:
- The size of the illuminated field is usually comparatively small and artificial vision systems are often quite expensive, so the cost of the light source is usually a minor concern. However, it may not be easy to replace a broken light source within a complex machine; in this case the long service life of the leds is a benefit.
- The components of the LEDs tend to be small and can be placed with high density on flat or uniform surface substrates (PCBs, etc.) so that light and homogeneous sources that direct light from controlled directions can be designed in inspected parts. This can often be obtained with low-cost, small lenses and diffusers, helping to achieve high light densities with control over lighting and homogeneity levels. The led fonts can be configured in several forms (lights for reflective lighting, coaxial lighting ring lights, background lights for contour lighting, linear assemblies, large format flat panels, dome sources for diffuse omnidirectional lighting).
- LEDs can easily be stroboscopic (in the microsecond range and below) and synchronized with images. High power LEDs are available to allow well-lit images, even with very short light pulses. This is often used to obtain sharp and sharp images of the rapidly moving parts.
- The LEDs come in various colors and wavelengths, allowing easy use of the best color for each need, where the different color can provide better visibility of features of the interest. Having a precisely known spectrum allows you to use closely matched filters to separate the information bandwidth or to reduce the disturbing effects of ambient light. LEDs usually operate at comparatively low working temperatures, simplifying heat management and dissipation. This allows the use of plastic lenses, filters and diffusers. Waterproof units can also be easily designed, allowing use in harsh or humid environments (food, drink, oil industries).
Medicine and Biology
Health care has echoed the advantages of LEDs over other types of lighting and has incorporated them into its state-of-the-art equipment. The advantages offered by LEDs in their current state of development have led to their rapid diffusion in the world of instruments for diagnosis and support in medical and surgical procedures. The advantages appreciated by medical professionals are the following:
- The small size of light sources that, in general, may be associated with very thin and flexible light guides allowing them to travel through the inside of also thin catheters.
- The absence of accompanying infrared radiation, allowing them to be associated with the qualification cold light. The heat released by other types of light sources made it difficult to use in certain diagnostic observations or surgical interventions.
- The white tonality that is usually prescribed for medical observations. It should be a natural white color capable of presenting all colors without metamerism problems. The natural color of the thus illuminated tissues thus favors the correct diagnosis of the observed field.
- The high luminous intensity reached by these light sources.
Diagnosis and vision
Based on the above ideas, current endoscopes are equipped with led lighting. The endoscopic technique covers many medical specialties, for example gastroscopy, colonoscopy, laryngoscopy, otoscopy or arthroscopy. All these techniques allow the observation of organs and systems of the human body through the use of miniature video cameras. They can also be used in surgical interventions or to make diagnoses. The equipment is also known as video scopes or video endoscopes. There are rigid or flexible depending on the needs. Fiber optics adapts to each particular case. On the other hand, the luminaires in the operating rooms and dental clinics are currently LED. They perfectly satisfy all the technical and sanitary requirements for their use. Obtaining bright, natural, white lighting (more than one hundred and fifty thousand candles at a distance of one meter from the field of operation), without shadows and without infrared or ultraviolet emissions that could affect both the patient and the medical staff, is especially appreciated. who participates in the intervention.
The same thing happens with the front lamps of surgeons and dentists equipped with LEDs, with lamps for medical examinations, for explorations and ophthalmological interventions or for minor surgery, with which it can be affirmed that LEDs have come to cover all the medical specialties. Optical companies dedicated to medicine have incorporated LEDs into their observation equipment, for example in microscopes, thereby obtaining many advantages for the study of images using different techniques (brightfield, contrast, fluorescence), which highlights manifesto in the advertising and commercial fields. LEDs are successfully used as sensors in heart rate monitors or oxygen sphygmomanometers to measure oxygen saturation.
Therapy
LED light is used in a skin treatment technique called phototherapy. Remember that the light emitted by the different semiconductor alloys is very monochromatic. Each of the colors (blue, yellow, red, etc.) is attributed a priority activity in a certain therapeutic process, for example, promoting healing (blue light), attacking a certain strain of bacteria (several colors), clarifying skin spots (red light), etc. Many materials and biological systems are sensitive or dependent on light. Grow lights use LEDs to increase photosynthesis in plants. Bacteria and viruses can be eliminated from water and other substances by sterilization with UV LEDs.
Industry
The industry has adapted the observation models used in medicine for its own needs and the equipment is called industrial endoscopes or also borescopes, flexoscopes or videoendoscopes. You can see with them the inside of machines, engines, ducts, cavities or weapons without having to disassemble them.
Other applications
The light from LEDs can be modulated very quickly, which is why they are widely used in fiber optics and free space optical communication. This includes remote controls used in LED televisions, VCRs and computers. Optical isolators use an LED combined with a photodiode or phototransistor to provide an electrically isolated signal path between two circuits. This is especially useful in medical equipment where signals from a low voltage sensor circuit (usually battery powered) in contact with a living organism must be electrically isolated from any possible electrical fault in a monitoring device operating at potentially dangerous voltages.. An optoisolator also allows information to be transferred between circuits that do not share a common ground potential.
Many sensor systems rely on light as a signal source. LEDs are often ideal as a light source due to the requirements of the sensors. LEDs are used as motion sensors, for example in optical computer mice. The Nintendo Wii sensor bar uses infrared LEDs. Pulse oximeters use them to measure oxygen saturation. Some tabletop scanners use RGB LED arrays instead of the typical cold cathode fluorescent lamp as their light source. Having independent control of three illuminated colors allows the scanner to be calibrated for more accurate color balance and there is no need for warm up. In addition, its sensors only need to be monochrome, since at any one time the scanned page is only illuminated by one color of light. Since LEDs can also be used as photodiodes, they can also be used for photo emission or detection. This could be used, for example, in a touch screen that registers light reflected from a finger or a stylus. Many materials and biological systems are sensitive to or dependent on light. Grow lights use LEDs to stimulate photosynthesis in plants, and bacteria and viruses can be killed in water and other substances using UV LEDs for sterilization.
LEDs have also been used as a quality voltage reference in electronic circuitry. Instead of a zener diode in low-voltage regulators, forward voltage drop can be used (for example, about 1.7V for a normal red led). Red LEDs have the flattest I/V curve. Although the forward voltage of the LED is much more dependent on current than a Zener diode, Zener diodes with breakdown voltages below 3 V are not widely available.
The progressive miniaturization of low-voltage lighting technology, such as LEDs and OLEDs, suitable for incorporation into thin materials, has encouraged experimentation in the combination of light sources and interior wallcovering surfaces. The new possibilities offered by these developments have led some designers and companies, such as Meystyle, Ingo Maurer, Lomox and Philips to research and develop proprietary LED wallpaper technologies, some of which are currently available for purchase. commercial. Other solutions exist mainly as prototypes or are in the process of being refined.
Contenido relacionado
Website colors
Active Server Pages
Enhanced Data Rates for GSM Evolution